Serialisation and Traceability: Knowing your implementation and expenditures
Posted: 6 February 2017 | | No comments yet
Pharma serialisation and traceability expert, Pasi Kemppainen, gives us his insights on how to ensure a future-proof and cost-effective strategy
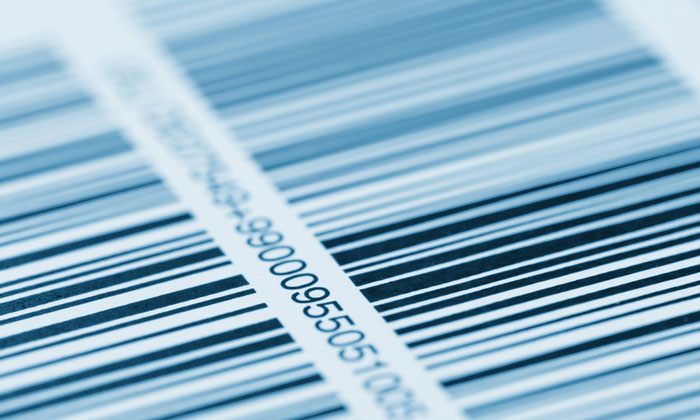
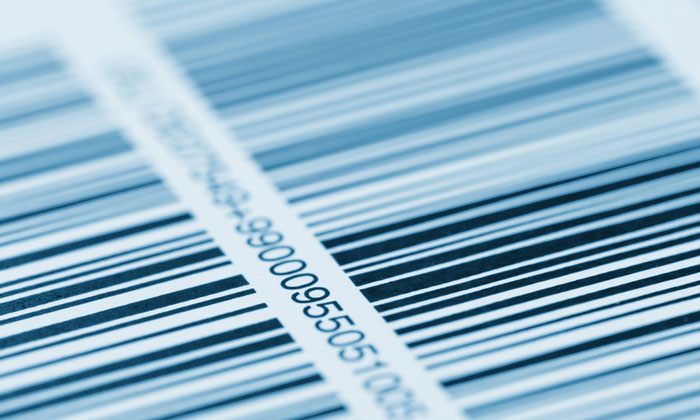
Some say that there are three categories of knowing. First of all, known knowns; there are things we know we know. We also know there are known unknowns; that is to say we know there are some things we do not know. But, there are also unknown unknowns – the ones we don’t know we don’t know. This characterises very well the pharma serialisation and traceability implementations and expenditures.
The time is nigh
It shouldn’t be a surprise to anyone in the pharma industry that the time is running out with the serialisation and traceability compliances for US and EU in November 2017 and February 2019, respectively. As a matter of fact, according to a recent survey by TraceLink, among 200 pharma companies globally, nearly 80% of respondents were concerned about hitting the deadlines. To put it bluntly, if you haven’t already started planning and projecting, you are taking a very high risk of not only losing the deadlines but also ending up paying more because of the delayed implementation.
Unfortunately, many pharma companies seem to still think that there is an unlimited delivery capacity from vendors, and the later implementation would end up in lower costs. Unfortunately, the opposite is true. There is no benefit in being a late mover anymore, if there ever was. This is bad news for almost half of the pharma companies who haven’t even started their projects yet according to IQPC Pharmaceutical Serialisation and Traceability 2016 Industry Report.
As the serialisation and traceability implementation in the regulated scope is, to the most extent, entirely new to the industry, there is understandably a lot of inexperience, unknowns and uncertainty with actually comprehending what is really required to comply with different markets. More than often, the thinking has been just to implement a low-cost print and verify add-on capabilities in the packaging lines with a simple serial number data transfer with a back-end IT system. And more than often, this has turned out not to be the case.
Well-planned is not half done
The conventional wisdom says that well-planned is half done. With serialisation and traceability this has turned out to be that well-planned is half of the problems solved. Often the implementation is seen to mainly focus on packaging line retrofitting, which is business as usual for pharma manufacturers. However, the implementation will also require new manufacturing and enterprise IT systems – and respective systems and data integration – which is especially new for the small and mid-size pharma companies. The true devil is in the implementation details and internal collaboration, and how to mitigate the execution risks and expenditures during, and more importantly, after the implementation.
When planning the serialisation and traceability strategy, it is fundamental to understand in detail how the different company operations, processes and systems will be affected. This not only helps to specify the required cross-company support for the implementation – and also the system and data dependencies – but also the total expenditures associated with the implementation. This can be an expensive process since the implementation requires resourcing and investments usually outside of the current budgets in the respective organisations.
For instance, master data and art work changes will require multiple organisations committing their resources and allocating costs for the implementation.
Compliance means expenditures
Image 1 illustrates the most common investments and cost elements in serialisation and traceability compliance implementations. While most of the elements are fairly self-explanatory and evident, there are some elements that are usually missed in the total implementation expenditures, especially project delays, OEE decrease, medicine verification service costs and supply chain integration.
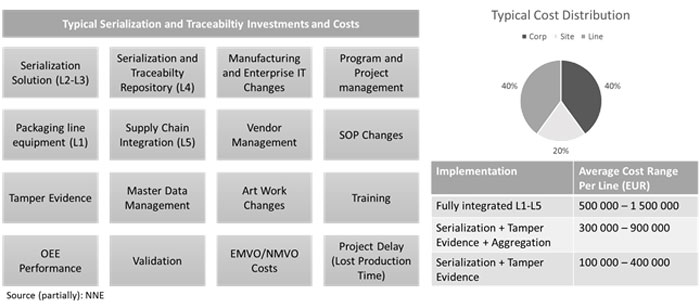
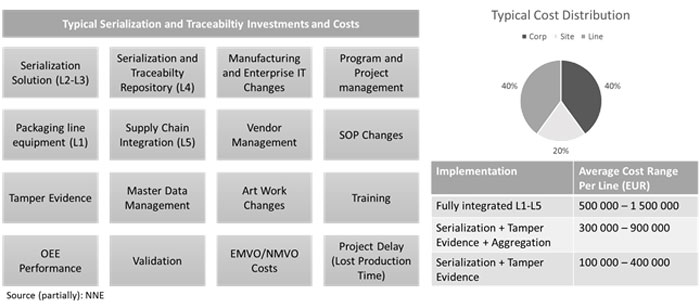
Typical serialisation and traceability investments and costs
The late stage changes in the solution requirements and specifications or rescheduled production planning might escalate into drastic increases in the total expenditures and especially in the readiness timetable. The larger and more organisationally distributed the company is, the more costs will be associated with the operational overhead due to the unclear governance with the responsibilities leading to a longer project implementation time. In addition, typically the implementations involve new vendors and equipment, which create additional risks with the validation and efficiency.
Consequently, as the shutdown period for the line validation and operator training are fixed very early on in the project planning, the project delays can lead, worst case scenario, to the product shortage, hence lost revenues and market share.
Overall Equipment Efficiency (OEE) decrease after the serialisation implementation can substantially increase the production costs especially in the longer term. OEE will not only affect the total line capacity but can also require upgrading the existing equipment with the new and more expensive equipment, after the implementation.
When combined with the potential requirement for aggregation, this can lead to changing from the manual packaging processes into automated solutions. In these cases, purchasing a completely new packaging line might be a smarter investment instead of retrofitting the current one. However, packaging line vendors might not have a delivery capacity available leading companies to stuck with the suboptimal solution with the respective risks.
Additionally, another often forgotten cost element is the annual EMVO/NMVO (European and National Medicine Verification Organisation) service costs which are based on the number countries where the company has Marketing Authorisation Holder registrations. For small pharma companies, this can cumulate on an annual basis as a substantial expenditure, even bigger than annual production OEE and supply chain integration costs. The bad news is that these costs are non-negotiable and hence a cost of making business decreasing the product margins.
Supply chain partners want their cut
Pharma business is highly networked with many supply chain partners in production, packaging, logistics and distribution. Unfortunately, the diverse serialisation and traceability regulations and partner requirements require varying engagement and reporting between the supply chain partners. In the US, the Drug Supply Chain Security Act requires supply chain partners to report product shipment transactions. Starting in November this year, the reports need to include the associated serial numbers. Although not required by the law, US wholesalers require aggregation reporting, which increases the complexity and costs of serialisation implementations and traceability reporting.
Even though the supply chain reporting is not required in EU Falsified Medicines Directive (FMD), it already seems inevitable that, at some point, EU wholesalers will require aggregation reporting, as in the US. This is simply to minimise the product handling and warehousing costs associated with the wholesalers’ FMD reporting requirements. This, in turn, increases the implementation expenditures in pharma manufacturing and IT, further affecting the product margins.
Another important source of supply chain integration costs is the contract packaging integration with Contract Manufacturing Organizations (CMO) or Contract Packaging Organisations (CPO). This is needed for the serial number provisioning from MAHs to the CMOs and CPOs, and for the batch reporting to MAHs for the regulatory reporting. Not surprisingly, a completely new IT platform, a serialisation and traceability repository, is needed to manage all this. The repository must also integrate with the existing company IT systems with the master data and supply network data.
It all adds up
All in all, serialisation and traceability investments and costs can sneakily add up substantially in the total cost of ownership over the years (see Image 2). When planning the strategy and respective investments, it is important to understand all the investments and costs associated with the end-to-end implementation, from the shop-floor up to the supply chain integration and regulatory costs. Some of the expenditures will only materialise during the implementation, such as the project delay and OEE costs, and mitigating them proactively is essential, as they tend to accumulate over time.
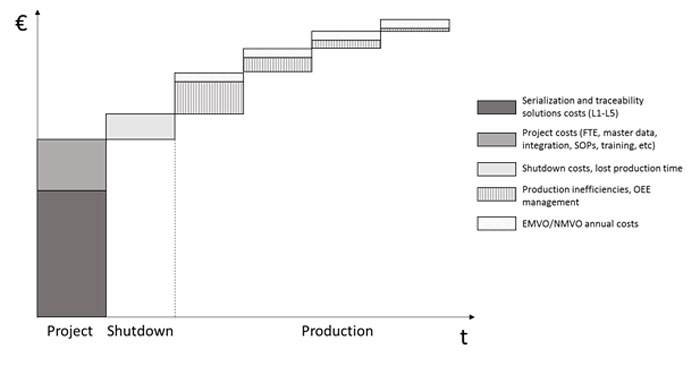
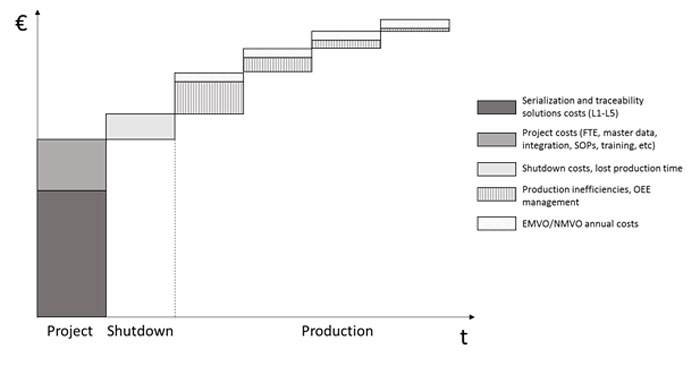
Total cost of ownership in serialisation and traceability implementations
Happy end?
Eventually, serialisation and traceability implementations can actually turn out to be packaging operations modernisation and IT renewal programs. It will provide a great opportunity to improve the current production operating procedures and rationalise the working at the packaging lines, potentially saving production time and resources in the future. The serialisation and traceability data can be used for improving business performance in reimbursement/chargeback programs, production analytics, supply chain management and facilitating innovations in patient care and clinical development.
In fact, serialisation and traceability pave the way for the first rudimentary industrial internet of things or Industry 4.0 implementation in pharma manufacturing, integrating the operations technologies at the packaging sites with manufacturing and enterprise information technologies. This might lead to more productive and cost-efficient pharma manufacturing and streamlined supply chain operations improving the business performance in the longer term.
Some say that beyond the three knowing categories there is also a fourth category, the unknown known, which we intentionally refuse to acknowledge that we know.