Exploring the advantages of PAT for pharmaceutical cleaning in Ireland
Posted: 4 May 2016 | | No comments yet
Process analytical technology (PAT) and its applications have been used in various industrial processes for a long time. It originates from the last century where its first application was in Germany after World War II within the chemical and petrochemical industry1. Following this, it was implemented and refined in different industries worldwide – for example in refineries and petrochemical plants – until it became an integral part of process control. However, it is considered a young technology in pharmaceutical manufacturing where the processes have always been restricted to conventional approaches. This forces many limitations on product quality monitoring since the control relies mainly on collected samples being tested off-line in a laboratory.
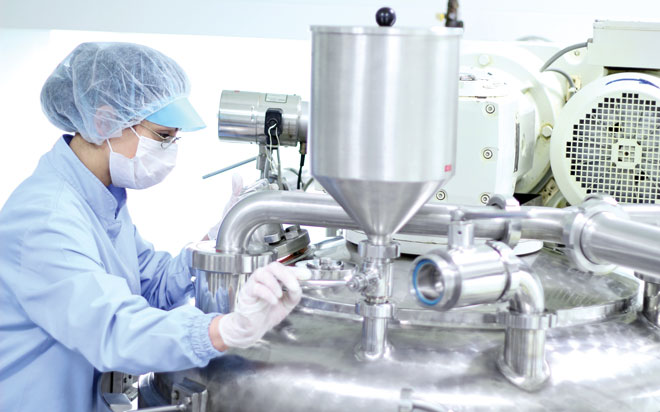
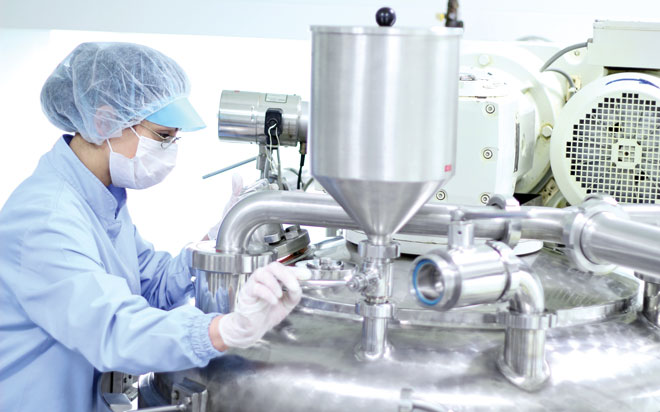
In order to support novelty in production, the United States Food and Drug Administration (FDA) started an initiative and set guidance in 2004 to describe PAT, its scientific scope and framework. PAT was defined as a “system for designing, analysing and controlling manufacturing through timely measurements (i.e., during processing) of critical quality and performance attributes of raw and in-process materials and processes, with the goal of ensuring final product quality”2. This regulatory scope fits into the broader Quality by Design (QbD) concept which requires the quality of a product to be designed in advance and not merely tested retrospectively. PAT’s main framework is to enhance understanding and control the manufacturing process to facilitate the implementation of QbD. Consequently, the effectiveness of a process can be improved using PAT tools, such as process analysers, process control tools and multivariate tools. This allows for an improved study of the effect of critical sources of variabilities on the product quality in real time, as well as providing a good insight on how to manage the effect of product composition and other factors on quality (multivariate) as opposed to traditional univariate trend analysis2-4.
The advantages of PAT as an industrial monitoring tool cannot be over-emphasised; it is rapid and non-destructive and imparts more understanding into a process, thus engendering greater confidence in the quality of the end product5-6. Furthermore, when PAT is deployed the need to develop chemometric models for both qualitative and quantitative testing are not commonly required as, compared with data analysis during process development, the more important aspect is the capability to monitor the underlying process in situ or in near real time7.
Many of the recent applications of PAT in the pharmaceutical industry are limited to research and development (R&D) and, to a lesser degree, scale-up which involves transferring the manufacture of the product from the lab scale through pilot plant to industrial-scale production7. This is likely due not only to the greater regulatory and safety restrictions, but ironically also to the greater process understanding being gained during R&D and scale-up as a result of the QbD initiative, which reduces the benefits of PAT at a manufacturing scale8.
Nevertheless, well established examples of PAT application at all stages of pharmaceutical manufacturing are outlined as follows.
One of the first steps in manufacturing is identification of raw materials. Here, handheld Raman (and, to a lesser extent, near-infrared and mid-infrared; MIR) spectroscopes are well established tools for fast and accurate material identification9. Raman spectra can be obtained directly through transparent containers such as glass and many plastics, and their quality sometimes matches those obtained by full-scale Raman spectroscopes. Within a few seconds or minutes, the operator will receive a statistically-validated result through comparison with either a single reference spectrum (in the case of a known sample) or a library (unknown samples)10.
For several new chemical entities, GlaxoSmithKline uses in situ, on-line MIR and ultra violet spectroscopies to monitor reactions and create in-depth process understanding8.
In the synthesis of a particular active pharmaceutical ingredient (API), a reactive step was originally thought to be initiated by the addition of a catalyst, as confirmed by off-line analysis9. However, when the reaction was later monitored in-line (in situ) by MIR using a silver halide probe, it was discovered that the addition of the catalyst did not itself start the reaction. Rather, during off-line analysis the catalyst was shown to have been activated by the water used to prepare the sample for high-performance liquid chromatography analysis.
Drying can be understood and optimised using PAT to reduce drying cycle time and increase process control. Off-line loss on drying (LOD) is the traditional way to monitor the drying process, however, it can be difficult and time-consuming, particularly in manufacturing environments. In response a particular API manufacturing plant developed an on-line mass spectrometric method to determine the drying end-point of an API in a vacuum paddle dryer11.
The mass spectrometer was fitted to the gas exit of the dryer to measure the escaping solvent partial pressure. The partial pressure corresponding to the drying end-point was first determined by collecting corresponding off-line LOD data, and then the mass spectrometer data output was connected to the central control room, where the drying process is automatically stopped once this validated partial pressure is reached.
Continuous secondary manufacture usually requires the implementation of PAT for monitoring multiple Critical Quality Attributes and Critical Process Parameters. One vendor company, GEA, currently offers the only complete integrated secondary processing solutions for oral solid dosage production. The ConSigmaTM line ranges from continuous direct compression systems, comprised of continuous powder feeding, blending and tablet compression, to continuous wet granulation ones, where continuous wet granulation and semi-continuous drying are inserted between the blending and tabletting steps.
In one of many PAT applications in this system, GEA have developed their own fibre-optic Lighthouse ProbeTM for on-line spectroscopic measurements. For example, FT-NIR is used in ConSigmaTM to monitor the moisture of drying granules on-line, which has been thoroughly validated to be at least as accurate as off-line Karl Fisher analysis12.
Why the delay?
With the tremendous improvements made by the application of PAT to various pharmaceutical technology/manufacturing processes, as typified by the examples just described, it does beg the question why it has not already been previously deployed for monitoring streams during pharmaceutical cleaning? Especially now that the global pharmaceutical industry is experiencing gloomy financial constraints; as seen by the recent decision of Swiss pharma giant, Roche Holding AG, to shut down/sell its manufacturing plant in Clarecastle, Ireland, in order to invest in more profitable new/emerging technologies13.
Furthermore, regulatory requirements regarding pharmaceutical cleaning validation have become more rigorous14, thereby necessitating the need for a greener, faster and less expensive approach to cleaning protocols.
Here at the Pharmaceutical Manufacturing Technology Centre (PMTC), Ireland, we are currently working alongside Britest Ltd UK to develop methodologies that can address generic and specific issues relating to pharmaceutical cleaning. PMTC was established in December 2013 and funded both by Enterprise Ireland and IDA Ireland, supplemented with co-funding from industry and other public sources. Its mission is to make Ireland the global hub of pharmaceutical process innovation and advanced manufacturing.
It also shares a common vision with other technology and research centres by helping to support and develop the Irish pharmaceutical industry (API and drug substances). Companies access PMTC to create projects and execute world class industry-relevant research in advanced technology solutions to address contemporary manufacturing issues.
In collaboration with leading pharmaceutical companies, PMTC currently has six main themes of research: cleaning, validation and verification; enabling and control of continuous processing; soft sensor modelling tools; API real-time release PAT; powder processing and advanced rapid micro-analytical techniques.
In response to developments in the regulatory environment relating to cleaning validation, PMTC commissioned the ‘compliance group’ to deliver a Good Cleaning Validation Practice document. This document was produced based on a review of current guidelines and input from Ireland’s Health Products Regulatory Authority and industry, and is available online (www.pmtc.ie). Currently headed by Dr. Chris Edlin, the centre’s director, the PMTC’s vision in collaboration with its members and partners is to develop its reputation as a world-class centre of excellence for pharmaceutical manufacturing issues, with the ability to attract significant future R&D funding from both industrial and EU/National funding agencies.
This entails the use of Raman spectroscopy (in the transmission geometry) as a PAT tool; to monitor solvent purity during cleaning. This approach will afford the additional advantage of being able to ascertain the exact amount of solvent required during cleaning procedures and thus limit excessive solvent usage as well shorten cleaning time. It will also help with choosing the right solvent for any particular cleaning process, thus helping to automate the cleaning protocols once parameters such as solvent volume and cleaning time have been properly estimated.
This project has already drawn interest from a wide range of industrial giants; from API manufacturers and drug products producers to makers of fine chemicals. We also plan to extend these studies into the dairy and food industries. Results from the initial analysis are expected to be published in the summer of next year and will make a significant contribution towards ameliorating the current constraints experienced by pharmaceutical companies during cleaning.
References
- Bakeev, KA. Process analytical technology: spectroscopic tools and implementation strategies for the chemical and pharmaceutical industries. John Wiley & Sons: 2010
- FDA, Guidance for Industry PAT-A Framework for Innovative Pharmaceutical Manufacturing and Quality Assurance, FDA, 2004
- Pierre-Francois Chavez et al. Active content determination of pharmaceutical tablets using near infrared spectroscopy as Process Analytical Technology tool. Talanta. 2015; (144), 1352-1359
- International Conference on Harmonization (ICH) of Technical Requirements for Registration of Pharmaceuticals for Human Use, Topic Q8 (R2): Pharmaceutical Development, Geneva, 2009
- Tingting Peng et al. Study progression in application of process analytical technologies on film coating. Asian journal of pharmaceutical sciences. 2015; (10), 176-185
- Muller J, Knop K, Thies J, et al. Feasibility of Raman spectroscopy as PAT tool in active coating. Drug Dev. Ind. Pharm. 2010; (36) 234-243
- George L. Reid, Howard W. Ward II, Andrew S. Palm, Koji Muteki, Process Analytical Technology (PAT) in Pharmaceutical Development, (2012) published online in ‘The Review of American Pharmaceutical Business & Technology’
- Simon, L. L. et al. Assessment of Recent Process Analytical Technology (PAT) Trends: A Multiauthor Review. Organic Process Research & Development. 2015; (19), 3–62
- Chanda, A. et al. Industry Perspectives on Process Analytical Technology: Tools and Applications in API Development. Organic Process Research & Development. 2015; 19, 63–83
- Bakeev, K., Chimenti, R. Pros and cons of using correlation versus multivariate algorithms for material identification via handheld spectroscopy. European Pharmaceutical Review (2013)
- Bordawekar, S., Chanda, A., Daly, A. M. Industry perspectives on process analytical technology: Tools and applications in API manufacturing. Organic Process Research & Development. 2015; (19), 1174–1185
- Fonteyne, M. et al. NIR spectroscopic method for the in-line moisture assessment during drying in a six-segmented fluid bed dryer of a continuous tablet production line: Validation of quantifying abilities and uncertainty assessment. J. Pharm. Biomed. Anal. 2014; 100, 21–27
- Published online in the ‘TheJournal.ie’ http://businessetc.thejournal.ie/job-losses-clare-2-2441463-Nov2015/?utm_source=shortlink
- European Medicine Agency (EMA), ICH 2015 guideline Q7 on good manufacturing practice for active pharmaceutical ingredients EMA/CHMP/ICH/468930/2015
Biographies
Adeyinka Aina is a member of the Royal Society of Chemistry (RSC), UK. He obtained his doctoral degree from the prestigious School of Pharmacy, University of Nottingham, UK. He has extensive professional experience in both teaching and scientific research, having worked in Nigeria, China, Singapore, England, Malaysia and in Iraq.
Manuel Kuhs completed his PhD on pharmaceutical crystallisation in 2015 at the University of Limerick, Ireland, where he is now employed as a postdoctoral researcher in the Bernal Powder Engineering Research Group. His primary research interest is in developing a mechanistic understanding of granulation in continuous twin screw wet granulation.
Shaza Darwish completed her dual degree in Chemistry and Chemical Engineering at the American University of Beirut in 2014. Currently she is a PhD student at University of Limerick working under the supervision of Professor Gavin Walker. Her research mainly focuses on model predictive control of continuous pharmaceutical processes.
Dr. Chris Edlin is the Director of the PMTC where he is responsible for the overall direction and management of the research in the Centre. He takes a leadership role in fostering pharmaceutical manufacturing research at a national and international level, in conjunction with industrial and academic partners, and funding agencies.
The rest of this article is restricted - login or subscribe free to access
Why subscribe? Join our growing community of thousands of industry professionals and gain access to:
- bi-monthly issues in print and/or digital format
- case studies, whitepapers, webinars and industry-leading content
- breaking news and features
- our extensive online archive of thousands of articles and years of past issues
- ...And it's all free!
Click here to Subscribe today Login here