Breaking down silos – how digital tools can transform pharma manufacturing
Posted: 15 July 2025 | Adam Cross (Hexagon), European Pharmaceutical Review | No comments yet
Following their recent LinkedIn Live, Hexagon’s Adam Cross, Industry Director for Pharma and Life Sciences, reveals the state of data in pharmaceutical manufacturing, the opportunities available and how companies can ensure success and sustainable outcomes in their digitalisation journey.
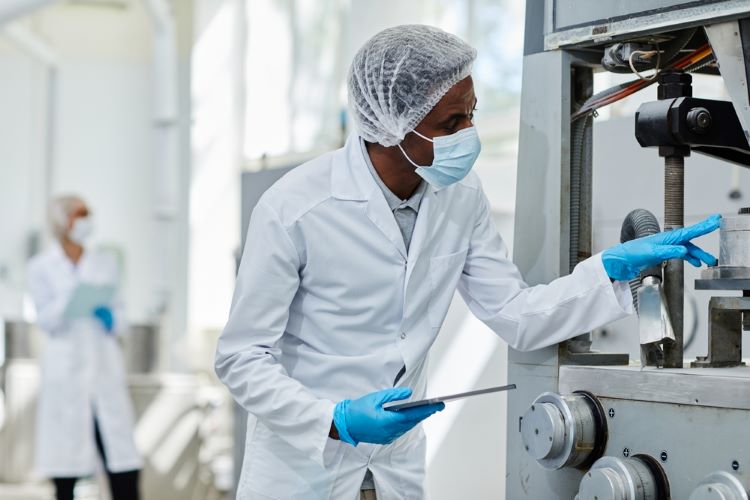
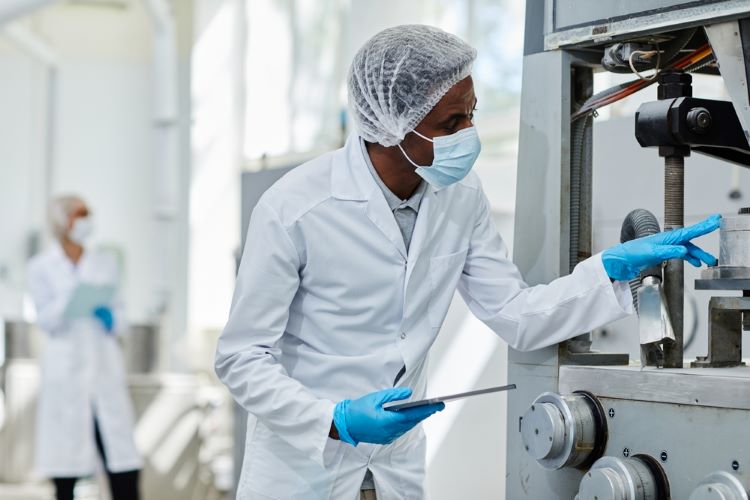
New research reveals that while 52 percent of pharmaceutical companies remain in early stages of digitalisation, leading manufacturers are finding innovative ways to overcome data fragmentation and drive operational efficiency. The pharmaceutical manufacturing sector stands at a digital crossroads.
Despite significant investment in modern technologies, more than half of companies are still struggling with the fundamentals of digitalisation, according to recent research conducted by Hexagon in partnership with Forrester Consulting.
In a recent LinkedIn Live, Ian Betteridge of European Pharmaceutical Review met with Adam Cross, Industry Director for Pharma and Life Sciences at Hexagon to discuss the state of data in the industry.
The data challenge
The research reveals a stark reality: 80 percent of pharmaceutical organisations surveyed report serious problems with either the availability or quality of data and documentation. This fundamental challenge is creating a perception that companies are lagging in their digitalisation efforts, despite substantial technology investments.
Interestingly, quite a lot of respondents reported a gap in skills and knowledge of modern digital tools and what those technologies can bring to an organisation”
Cross explains that the industry faces a complex web of challenges. “There was definitely a perceived risk of changing the ways of working practices. Interestingly, quite a lot of respondents reported a gap in skills and knowledge of modern digital tools and what those technologies can bring to an organisation,” he notes.
When these compliance concerns combine with skills gaps, Cross observes that “the status quo can seem like a friendly place to remain.” Paradoxically, many transformations are being driven by external factors such as technology end-of-life cycles rather than proactive strategies to leverage digital capabilities for competitive advantage.
The environmental imperative
Sustainability has emerged as a key driver for digital adoption, with 76 percent of organisations already investing in tools to better plan sustainable disposal and decommissioning of facilities. More significantly, 73 percent of companies report seeing reduced carbon footprints through technology adoption.
73 percent of companies report seeing reduced carbon footprints through technology adoption”
The opportunity lies in comprehensive asset lifecycle management. By leveraging digital tools to monitor energy consumption and operational efficiency, manufacturers can address the operational costs that typically represent 60-80 percent of an asset’s total lifecycle expenditure. As Cross explains: “By being able to leverage digital tools, and particularly now that you’ve got new facilities, new assets, and obviously new kinds of operational technologies and ways of being able to monitor and control processes, these organisations have much better access to information and data about what kind of energy a particular asset or a particular process line is drawing.”
This dual benefit of environmental responsibility and financial efficiency is proving compelling, as Cross notes: “So not only can you keep your carbon footprint low, but you can keep your CFO happy.”
The silo problem persists
Despite widespread recognition of the issue, data silos continue to plague pharmaceutical manufacturing. The research found that 68 percent of respondents believe data fragmentation is hindering their decision-making capabilities.
Cross identifies three primary drivers behind this. First, “tick-box thinking” where “there is a requirement to create some sort of digital system that captures something, it’s brought in, [and] it does what it needs to do.”
Second, “technology first thinking” where there’s “a clamour or a desire from up on high to use tools like AI or machine learning or digital twin or whatever it might be, without ever really getting to a kind of a point or place where you understand the value that tool or technology might bring.”
Third, organisational challenges where companies struggle to “either agree or prioritise what the opportunity might be to leverage some of these digital tools to drive value and create business impact.”
The compliance-driven nature of the industry exacerbates these challenges. Cross describes how “once you’ve validated it, what happens is that becomes a sealed box” and organisations then face the question: “do we reopen the box that we just sealed that is designed to do this and could possibly do what else we need to do?” This thinking, he notes, has led to “some sort of Frankenstein’s monster, with different pockets of capability where some may speak to each other and some may not.”
Operational impact
The real-world consequences of fragmented workflows are substantial. Cross shares a compelling case study: “They looked at one site, and at how long it actually takes to carry out a piece of maintenance? What they worked out is that on average, the time on tools was about three hours. The total time it was taking to execute the work order, though, was something like 14 hours.” He identified that “there was about 11 hours of non-value added administrative tasks, because you were trying to, in the first instance, plan and schedule and understand upfront what was needed from lots of different systems that didn’t necessarily talk to each other.”
This inefficiency extends to compliance activities, where just over half of companies struggle to maintain efficiency during audits. The challenge lies in aggregating data from disparate systems to demonstrate process control to regulators.
Digital twins and real-time monitoring
Leading manufacturers are addressing these challenges through sophisticated digital twins combined with real-time monitoring capabilities. Cross explains that “regardless of whether you are just trying to create a basic digital twin or whether you’re looking to introduce real-time monitoring into that twin so that you can start to manage that process and you can start to make sure that the equipment is within tolerance and the process is within tolerance, the benefits are huge.”
These technologies create environments where compliance information can be stored, digitised, and validated in context, transforming weeks of manual data preparation into minutes of automated reporting.
As Cross notes: “You’re almost certainly circumnavigating weeks of manual data preparation. What was once a manual task to go across all of these different systems and filing cabinets to try and find the information you need can now be achieved in a matter of minutes with a couple of clicks.”
The benefits extend beyond efficiency gains. Digital twins provide inspectors with comprehensive visibility into manufacturing processes, offering evidence that systems are under control while building confidence in the organisation’s quality management capabilities.
Building trust through iteration
The most successful digitalisation approaches follow what Cross calls a “crawl, walk, run” methodology. He advocates that “organisations should be looking at how they can leverage these digital tools in an iterative manner” rather than attempting comprehensive overhauls.
The most successful digitalisation approaches…leverage these digital tools in an iterative manner” rather than attempting comprehensive overhauls”
Cross emphasises that “organisations have only got a certain tolerance to change. And I think if you can mitigate that or if you can reduce that as much as possible and do it in bite size incremental chunks, it becomes much easier for you as an organisation.” This approach allows companies to prove processes, build user confidence, and continuously validate improvements whilst maintaining compliance standards.
The path forward
For companies beginning their digitalisation journey, Cross recommends a systematic approach: “Start with the end in mind. Spend the time upfront, do that assessment work, look at where you are as an organisation, look at what it is that you want to achieve, understand where you are and your maturity and your capability, the sort of foundational building blocks that you’re going to need and what do you have today.”
However, he stresses that assessment alone isn’t enough. “Go back and assess what value you’re actually realising from deploying this tool or technology and link it back to those first steps, that first plans that you made,” Cross advises. “Make sure that actually what you set the expected, forecasted, told the top floor you would generate as a result of this. Make sure that is what you are generating. And if you’re not, don’t be afraid to course correct.”
The pharmaceutical manufacturing industry’s digitalisation may be in its infancy but the companies that successfully break down silos and integrate their digital capabilities are positioning themselves for significant competitive advantages in efficiency, compliance, and sustainability.
Related topics
Clinical Development, Drug Manufacturing, Industry Insight, Manufacturing, Sustainability, Technology, Therapeutics