Galenic software implementation on a rotary tablet press: IMAGO and its functionalities
Posted: 3 March 2022 | Caterina Funaro (IMA), Federica Giatti (IMA Active), FS Consoli (IMA), Leo Di Carlo (IMA), Marco Minardi (IMA), Nicola Pistillo (IMA) | No comments yet
In this article by IMA, discover how IMAGO software installed on rotary tablet presses supports scientists during tablet manufacturing, providing critical insights into powders.
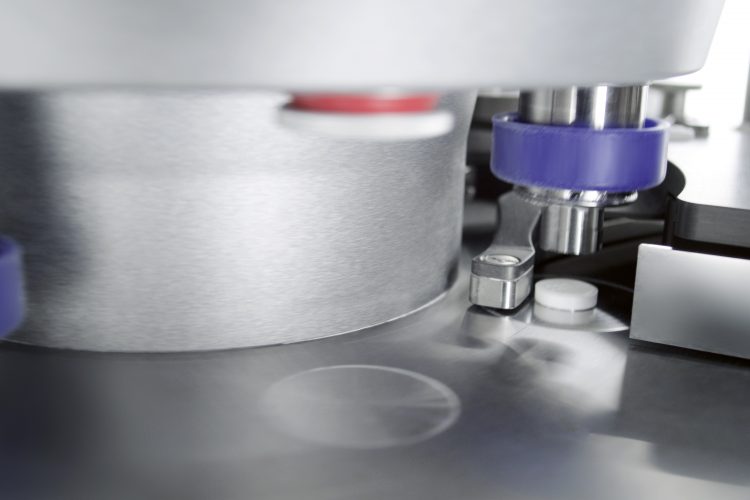
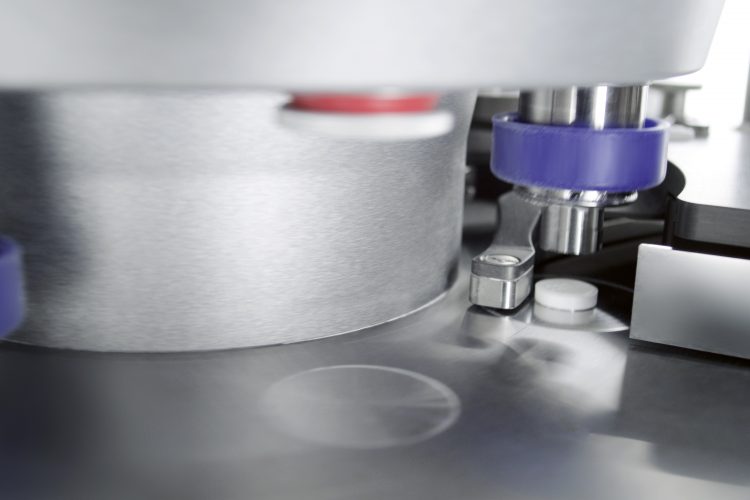
Introduction
It is not possible to set boundaries for an industrial software. It is so volatile that it is difficult to define its application field and its competences in industry today, since a boundary cannot be defined for something that is continuously improving and evolving.
But it is possible to define an evolutionary trend for the industrial software world, and that is what Acatech (National Academy of Science and Engineering) has done by creating the six-stage maturity model, known as Industry 4.0 Maturity Index.1
The industrial evolution trend of this model is going from digitalisation to industry 4.0, the future industry in which equipment and automation are perfectly integrated. Managers will need data to extrapolate information and make important and more conscious decisions, based on real data and not only on assumptions. Industry 4.0 is also synonymous with forecasting and minimising mistakes, but that is not all: the working day of machine final users should be improved and facilitated by giving them the instruments that meet their needs.
IMA, as a market leader in automatic machines, studies the shape of new industry and is taking steps towards the future industrial reality, beyond companies’ Industry 4.0 abilities today, by launching IMAGO.
The aim of this article is to explore IMAGO’s abilities, with a focus on its inner structure as well as on its functionalities, implemented thanks to our close collaboration with our partners OSI-Soft and Ematica.2
IMAGO development: why and how
IMAGO is a Galenic software, based on the revolutionary Kortex-Max control system of the new generation of IMA tablet press machines as well described in reference 3.3 IMAGO goes beyond the Galenic world. Created by the combined forces of software, mechanical experts and people working in pharmaceutical tableting R&D, IMAGO is a tool designed for scientific people.
It is a completely integrated platform that allows a huge amount of data to be extracted automatically, presented, aggregated and made ready-to-use for the final user.
Basically, its functionality is to help in all steps of powder manufacturing:
- Analysing tableting process parameters
- Studying powder behaviour under tableting
- Understanding the influences of tableting process parameters even on the formulation as well as on the tablets
- Providing strong information about the scale-up approach from a pilot scale to industrial equipment.
It is well known4,5,6 that powder behaviour under tableting is a complex world which the technologist or formulator has to face during tablet manufacturing. The brittle, plastic or elastic tendency of a powder is really difficult to understand. Likewise, defining tablet press configuration, which maximises production output and maintains the high quality required by the market, involves a great effort by pharmaceutical companies, as does acquiring and storing data. Hence the first revolution of IMAGO is its intrinsic structure organisation. Starting from the Galenic process flow, the trial is set up directly on the tablet press (trial set-up), the data are acquired (data acquisition) and lastly, analysed (results analysis, Figure 1).
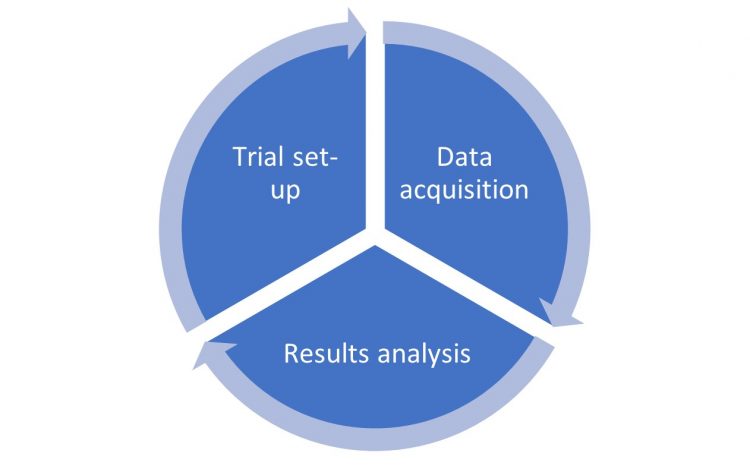
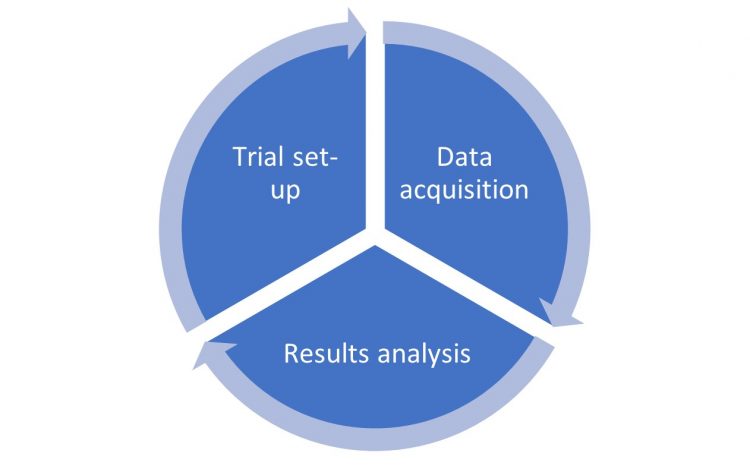
Figure 1: IMAGO process flow.
The user is completely followed by a guided procedure inserted in the HMI where information concerning the powder’s technological features (eg, bulk and tapped density, LOD), geometry information (eg, punch shape and dimension, surface area and dwell time) and process parameters (as a standard recipe in production application but removed of all unnecessary parameters) can be inserted.
This first step precedes the start of the trial in the tablet press: one of the innovative concepts of IMAGO is the way in which data is collected to be analysed subsequently. They are collected in a campaign, a “data region” created by the user that represents the main player in the analysis: within the same campaign, the user can upload all the formulations to be explored. Consistently, within the formulation, an infinite-number of tests can be performed. To give a real example, the formulator can investigate the behaviour of a specific active pharmaceutical ingredient (API, campaign), like ibuprofen, tested in different formulations (different excipient ratio). A single formulation can be then investigated at different compression forces (trials). This way of accumulating data allows for information to be acquired about the tableting process as well as about tablet characteristics, providing a strategy for easy and accurate visualisation.
The trials can now be started: the sensors already installed in the standard configuration of PREXIMA series (cells to detect forces) as well as the instrument for tablet characteristic monitoring communicate the final results to be first approved by the user and then sent in a dedicated external server directly connected to the machine. The logic behind the OSI UFL Connector extrapolates the raw information obtained from the trial just performed and packs it into the OSI PI Server, to guarantee its integrity and consistency. The raw data, indeed, has to be modelled to meet the needs of the final user, which can easily view them directly on a laptop, a tablet or a smartphone by connecting to the Google Chrome browser. The main advantage is flexibility: behind this structure (Figure 2), communication is fast, safe and really easy to understand.
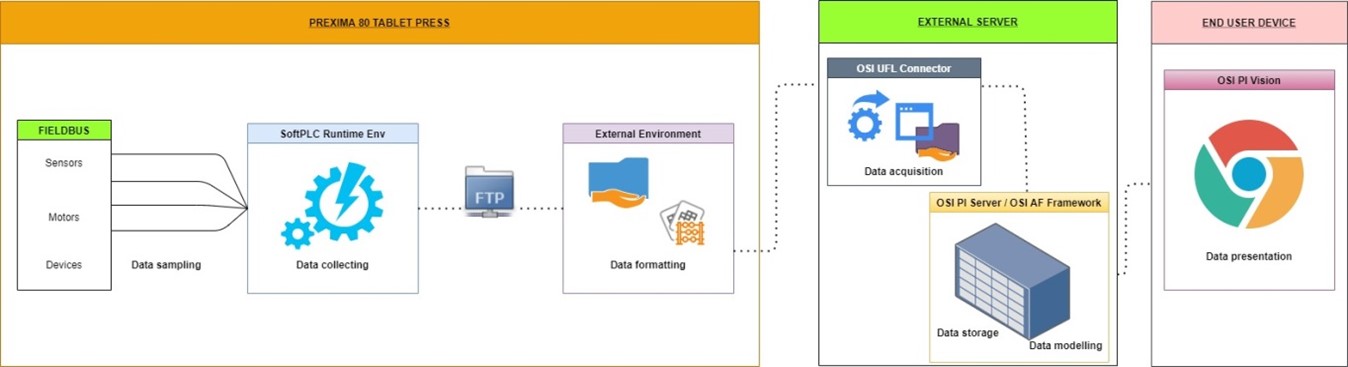
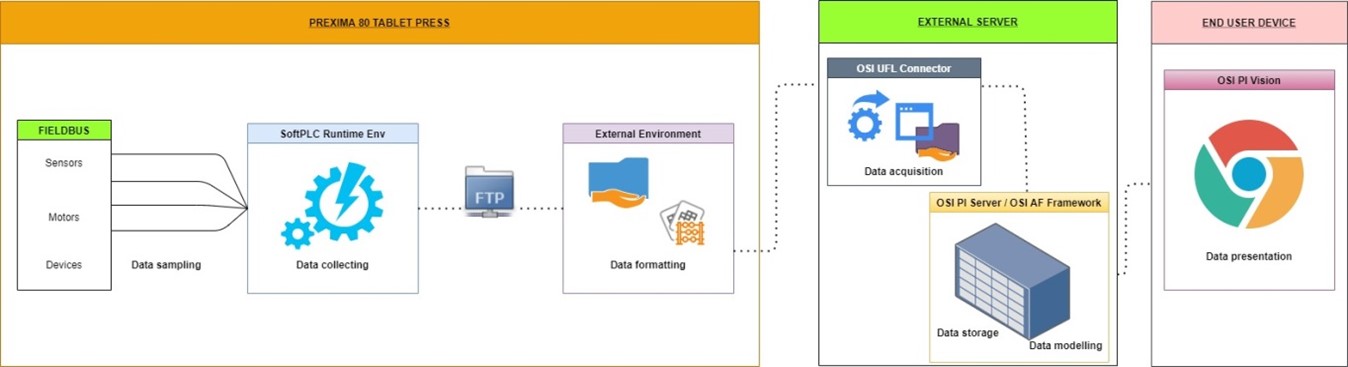
Figure 2: Data management process flow.
The final front-end of IMAGO, totally realised in OSI PI Vision, has been organised into four main macro areas: trials selection, tablet & tooling, force trend, and X-Y Analysis.
This organisation helps the user to define exactly what he is looking for: the trial selection area, indeed, is the research engine where it is possible to select the specific trials, formulations or campaigns to be investigated.
Tablet & tooling instead refers to all the tablet’s characteristics and geometry features: weight, thickness, diameter and hardness (with their relative average and standard deviation automatically calculated) as well as tensile strength, friability, porosity and solid fraction which are automatically calculated thanks to the data uploaded or manually written in the spaces provided (Figure 3).
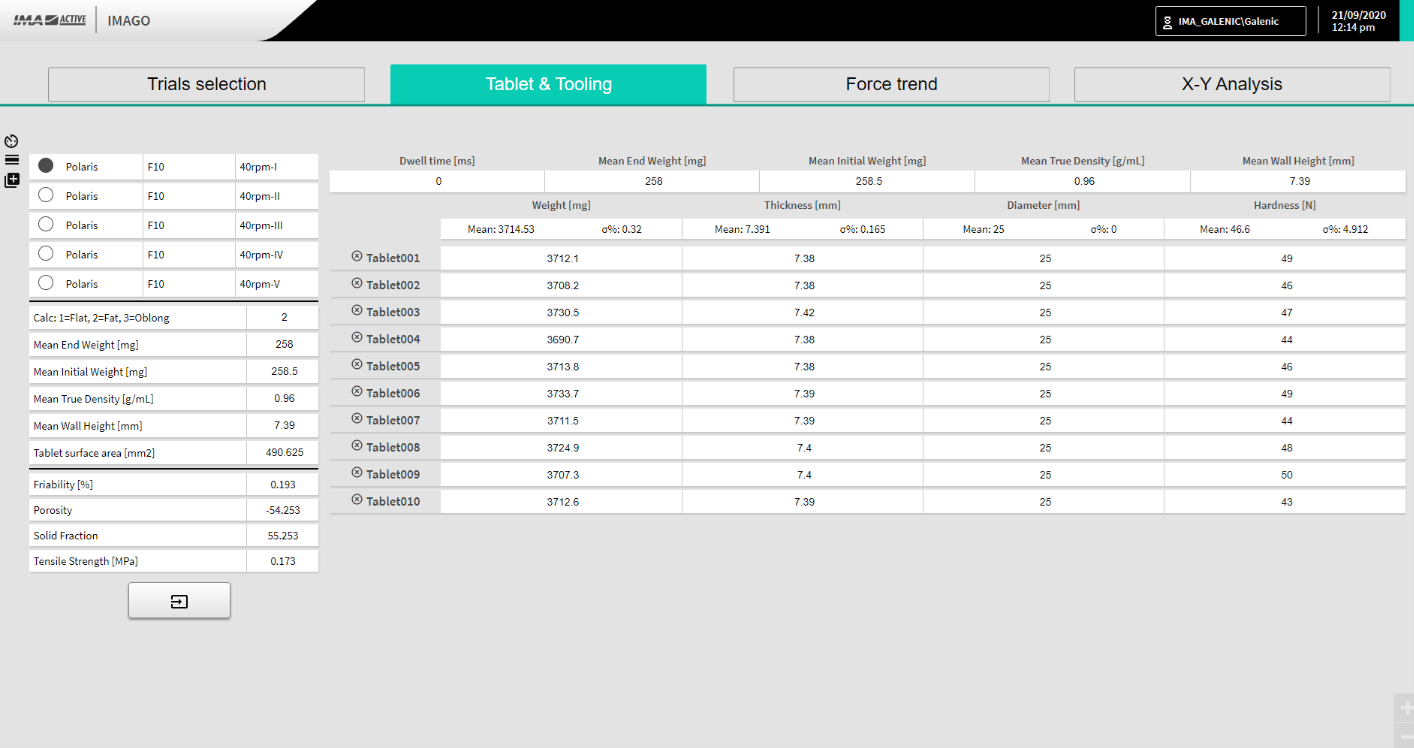
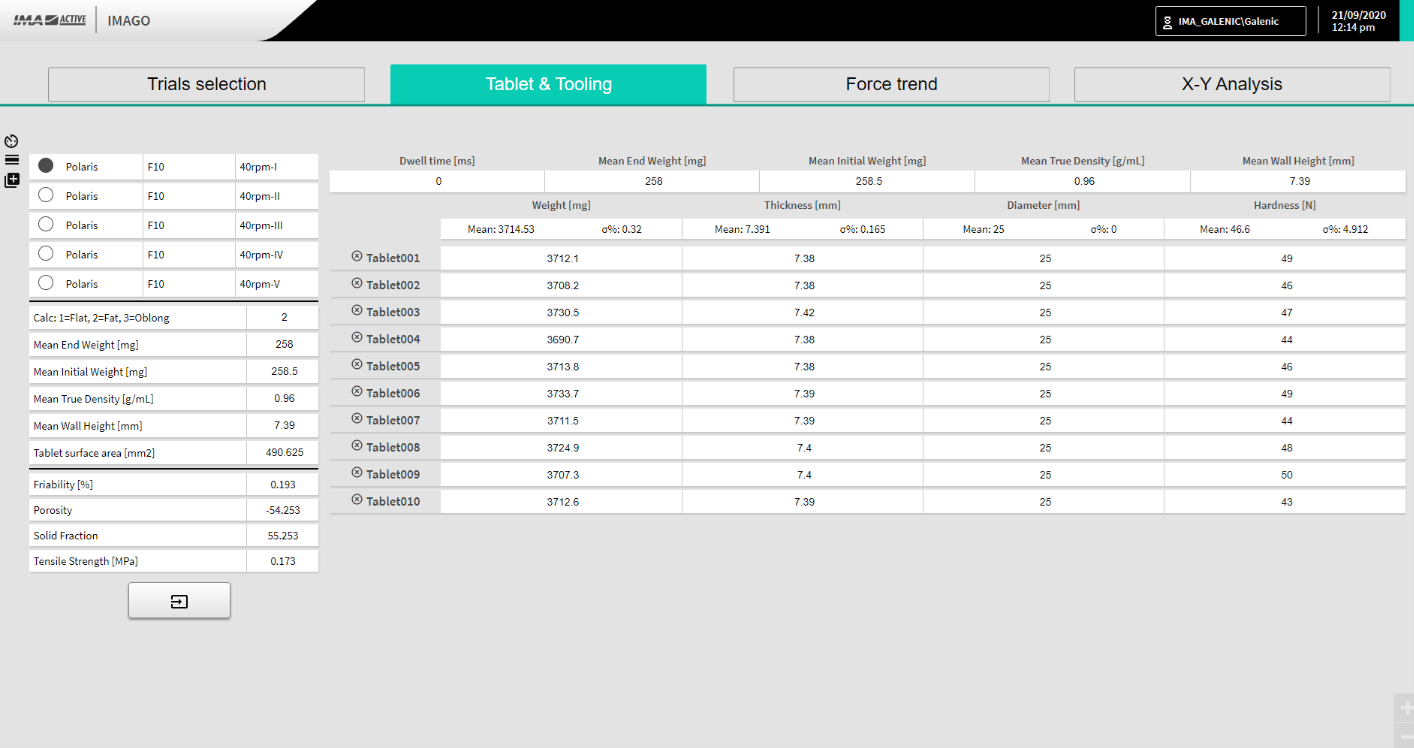
Figure 3: Tablet & Tooling macro area screenshot.
Forces trend is the macro area where all forces detected over the process can be compared and studied to gain useful information concerning the peak shape: its conformation can give the first indication concerning powder behaviour, always in an approach that compares different blends.
IMAGO is then able to provide the end user with graphs of the results, thanks to IMA’s experience in pharmaceutical processes and tableting. It is even possible to personalise the diagram itself based on the macro area “X-Y Analysis”, creating the data correlation of interest, and providing maximum flexibility in data characterisation for lab experts. Tabletability, compactability, compressibility, comparison between weight variation and paddle speed, or between ejection force and lubricant content are only some examples of the high flexibility of IMAGO.
Conclusions
IMAGO works as a primordial node of artificial intelligence, able to put data in the right form, ready for the end user to understand. This system can give real support in data analysis, making life easier for scientific people who have to face challenges in formulation development or improvement on a daily basis: tablet issues, production output improvement and excipient choices are the most common activities that require a high content of information to make the right decision without wasting time, money and materials.
IMAGO is able to collect the data directly provided by the tablet press machine, manually entered by the user, or automatically extrapolated by external devices, thus increasing the number of possible correlations and analyses. All these possibilities are already installed in IMA Laboratory on PREXIMA 80, the smallest scale rotary tablet press in the PREXIMA series. All these possibilities, extremely useful in powder understanding, which due to its complexity is difficult to predict, are already installed in a rotary tablet press so that the challenges of formulation development suitable for tableting can be considered right from the outset: flowability in dies, powder tabletability and processability.
IMA, with the extraordinary support of OSI-PI and Ematica, with IMAGO has created a model from university to pharmaceutical producers that permits experts to be aware of machine process and formulation development by putting the first milestone of this industrial r-evolution into the Industry 4.0 paradigm.
Authors
This article was written by Leo Di Carlo, Frederica Giatti, Nicola Pistillo and FS Consoli, Caterina Funaro and Marco Minardi at IMA.
References
- https://en.acatech.de/publication/industrie-4-0-maturity-index-managing-the-digital-transformation-of-companies/
- https://ima.it/pharma/ima-and-osisoft-setting-the-standard-in-table-process-data-to-accelerate-production-setup/
- https://ima.it/pharma/ima-active-chooses-ifix-hmi/
- Roberts J, Rowe RC. The compaction of pharmaceutical and other model materials – a pragmatic approach. Chemical Engineering Science 42 (1987) 903–911.
- Govedarica et al.. The use of single particle mechanical properties for predicting the compressibility of pharmaceutical materials. Powder Technology 225 (2012) 43–51.
- Santl M, Ilic I, Vrecer F, Baumgartner S. A compressibility and compactability study of real tableting mixtures: The impact of wet and dry granulation vs. direct tableting mixtures. International Journal of Pharmaceutics 414 (2011) 131–139.