Reinvention and knowledge transfer: Reviewing ISPE’s conference on Biotechnology
Posted: 17 November 2016 | | No comments yet
European Pharmaceutical Review brought you all the latest research and development live from the conference. Now read NNE Pharmaplan’s Leif Poulsen’s round up of the event…
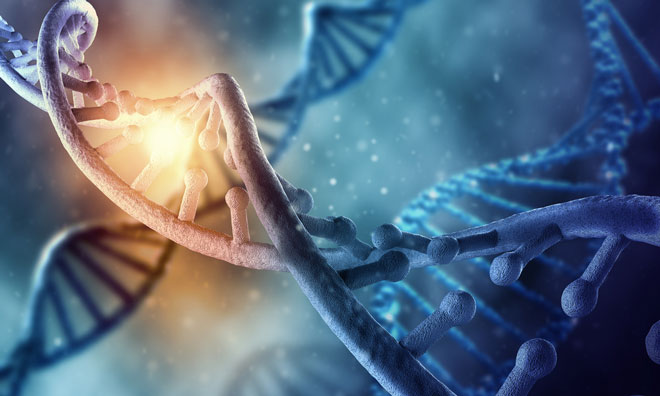
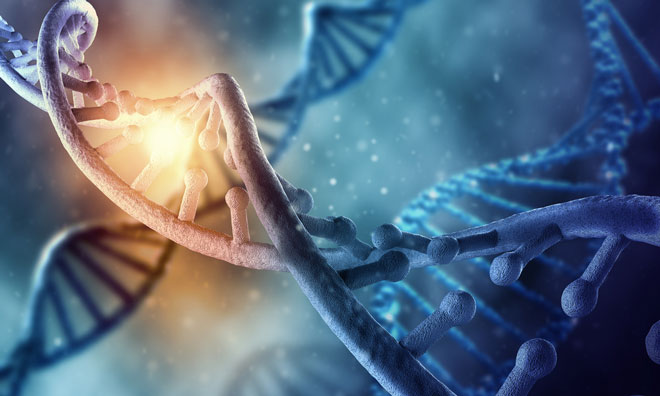
First, I have to say that I think the attendees this year were extremely knowledgeable people compared to many other conferences, I have attended. This was evident from the critical and qualified questions that were raised during the Q&A sessions after each presentation, which really led to some interesting and insightful discussions. So, I left this year’s ISPE Conference on Biotechnology feeling very inspired.
Process knowledge
I think the first presenter, an inspector from the HMRA in the UK, raised a very interesting and important point – namely that manufacturers tend to underestimate the level of process knowledge that the regulatory authorities and its inspectors possess. They are very well equipped to challenge the manufacturers on their processes. He thus encouraged manufacturers to be more open to dialogue with regulatory authorities. That goes for both established companies, which are generally hesitant to contact regulatory authorities, but certainly also start-ups, which he believes should initiate dialogue with regulatory authorities around their processes as early as possible to obtain valuable advice in the process design phase.
SESSION: QUALITY AND REGULATORY
Chairperson: Dr. Thomas Zimmer, VP European Operations, ISPE
13.20 – Biological Products, An Inspectors Point of View
Andrew Hopkins, Expert Inspector, MHRA
“…Is the current system fit for purpose? It’s not only about safe product but enough available safe product…fast but as safely as possible…it needs to be consistently manufactured…”
They have launched the MHRA Innovation office – set up by MHRA as part of the UK government’s industrial strategy for life sciences. It covers novel medicines, medical devices and processes used to manufacture these products. “A cross regulatory agency advice source…rather than having to go through so many different agencies you can sort it all out in one…
He then displayed his inspection findings, highlighting how the process is not always well defined and there are large knowledge gaps observed. “Training and knowledge are big things for me…I’m scared for us, for the industry, as we’re loosing a lot of knowledge…in the past, when it went wrong, you knew why. Now the knowledge isn’t there. that’s really one thing that worries me, knowledge management…”
Andrew Hopkins has been with the MHRA since March 2005 as a GMP Inspector and is currently the Chair person for the joint EMA and PIC/S working group regarding the potential update to EU GMP Annex 1. Prior to joining the Agency, he worked in the Pharmaceutical industry for approximately 20 years in positions including Quality Control, Quality Assurance and Production. Andew has a BSc Honours in Microbiology with Genetics and a Post Graduate Diploma in Industrial Pharmaceutical Science.”
Reinventing commercial biomanufacturing
The presentation which made the biggest impression on me, however, was given by Safaraz K. Niazi. Who talked about reinventing commercial biomanufacturing. Frustrated by the much too high prices of medicine today, he is completely rethinking the biotech process in an effort to bring down productions costs. Single-use, of course, is at the heart of the reinvention, but it goes well beyond that.
Safaraz K. Niazi, Founding Executive Chairman, Therapeutic Proteins International
Together with his team at Therapeutic Proteins International, he is scrutinising each step in the typical biomanufacturing process to see if it can be done differently. For instance, they have combined the processes of fermentation and recovery into one, reducing the number of tanks and eliminating centrifuges.
Likewise, they have brought down the need for pumps significantly by instead utilising something as simple (and cost-free) as gravity. By lifting and lowering single use bags to different levels, they can make the liquid substance run naturally through the process steps.
They have also taken a critical look at the bioreactor, in which large quantities of liquid, make it difficult to achieve a homogenous substance. They have solved this by placing the (medium-sized) single-use bags in a horizontal position. This leads to a lower fluid level, easing the process of homogenisation and making the stirrer obsolete.
HVAC systems is another area, where Therapeutic Proteins International has been able to reduce costs significantly. They have demonstrated that 80% of the HVAC is superfluous and have only one, where traditional biotech productions have four-five different systems.
FDA approval
I think everyone in the audience was thinking, ”that’s all very well, but can it be validated?”. But Mr. Niazi shot that doubt right down as he revealed that FDA has expressed clearly that validation shouldn’t be a problem. Interestingly, the start-up has been in close dialogue with FDA from the very beginning. So here, the HMRA inspector certainly has a great case to prove his point.
As an automation and IT professional myself, I also found the presentation from the two Boehringer Ingelheim executives on data science very interesting. Every biotech manufacturer knows the challenge of collecting sufficient data from small scale to correctly predict large scale.
SESSION: PROCESS SCIENCE
Chair: Christoph Herwig, Vienna University of Technology
08.30 – Data Science as Enabler for Scale-Up, Technology Transfer and Root Cause Analysis in Manufacturing
But Boehringer Ingelheim has developed a model to help them in this effort – and an additional model to help them assess how good they are at these predictions. A tool like this would be a godsend for any pharma/biotech manufacturer.
Finally, I just want to mention the visit to the Höchst industrial Park. The plants on the site were originally built for production of synthetic dye. Later it was transformed into a pharmaceutical site and now it is run as an open industry framework for about 90 companies. One of these, Sanofi, has taken over and enhanced the pharmaceutical facilities to produce the API for their entire insulin production. While I did not go on the tour inside the insulin production facilities, I did get a chance to go on a guided bus tour of the site. Particularly the administration building was an interesting visit. With its colourful walls, impressive height and expressionist style, it reminded me of a church and stands in stark contrast to the very clinical biotech industry. This was a great ending to a great conference.
Site Visit: Lantus (insulin) plant
Thank you to ISPE for putting together a highly relevant and diverse programme.
Leif Poulsen is a global technology partner within automation and IT in NNE Pharmaplan’s Global Best Practice group. His core competences lie within manufacturing execution systems and advanced automation and IT solutions and how they can support current and future business objectives. Poulsen is responsible for development of technology, methods and competences within automation and IT and works as a senior business consultant for customers worldwide. He is an expert on business analysis and conceptual design of automation and IT solutions.
16.00 – Knowledge Management within Pharmaceutical Engineering
Leif Poulsen, Partner, Global Consulting, Automation & IT, NNE Pharmaplan
“It’s hard to share knowledge with colleagues in different places…there is a language issue among other issues…but we have found something that is working…a common language to communicate…”
Poulsen highlighted the different strategies that NNE Pharmaplan have implemented:
Communtities of interest: “25 groups of professionals who share their knoweledge, make it accesible to customers through ‘our model’ – engineering model…benefits from single language and quick access to standards and guidelines as well as reference documents” Wiki: our encyclopedia, the handbook of ‘our model’ Connect: “It’s similar to Facebook – to have constant communication between industry workers…one forum for each question which you can then share knowledge and discussions through the stream…” Navigate: “We should embrace fresh new ideas from new young people starting in the industry AND we also need to show the history knowledge – this is a mentoring scheme to guide you through your first time period in the company…it’s to help you navigate your way” Peak: “Our training program…we want employees to become thought leaders within their field of expertise…and there is a continuous improvement cycle and continuous knowledge sharing”