Could CAR T therapies be manufactured in one day?
Posted: 30 March 2022 | Hannah Balfour (European Pharmaceutical Review) | No comments yet
New pre-clinical research suggests a 24-hour manufacturing process that produces fewer, more potent CAR T cells could be the key to both reducing production timelines and improving patient access to cell therapies.
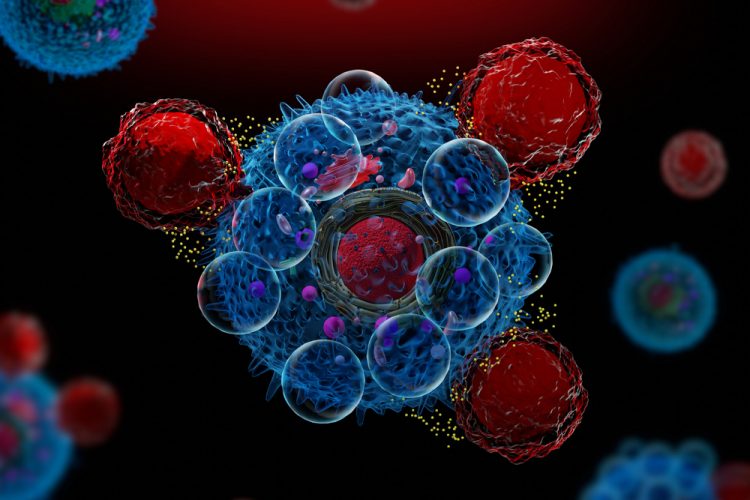
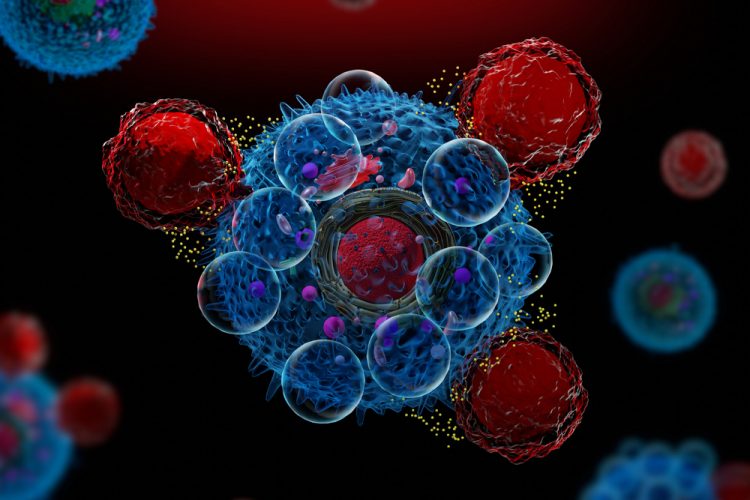
Typically, the cell manufacturing process for chimeric antigen receptor (CAR) T-cell therapies takes nine to 14 days; however, with a new technique, researchers at the University of Pennsylvania were able to produce functional CAR T cells with enhanced anti-tumour potency in just 24 hours.
An emerging form of immunotherapy, particularly in haematological cancers, autologous CAR T-cell therapies take a patient’s own immune T cells, modify them ex vivo with the addition of a CAR gene so they express receptors that better target cancer cells, then re-infusing them back into the patient. However, these treatments are well known for their lengthy production timelines, which can impact the cell’s ability to replicate and thus harm treatment potency, not to mention leave severely ill patients to decline while they await treatment. Therefore, a critical focus for autologous cell therapy manufacturers has been to reduce the time from blood extraction to modified cell re-infusion, also known as vein-to-vein time.
The pre-clinical study published in Nature Biomedical Engineering demonstrated that the time, materials and labour currently involved in producing CAR T cells could be vastly reduced. This, said the researchers, could be especially beneficial in patients with rapidly progressive disease and in resource-poor healthcare environments.
“While traditional manufacturing approaches used to create CAR T cells that take several days to weeks continue to work for patients with ‘liquid’ cancers such as leukaemia, there is still a significant need to reduce the time and cost of producing these complex therapies,” explained Dr Michael Milone, an associate professor of Pathology and Laboratory Medicine, and one of the co-leaders of the research at the Center for Cellular Immunotherapies, in the University of Pennsylvania’s Perelman School of Medicine. “Building on our research from 2018 that reduced the standard manufacturing approach to three days, and now to less than 24 hours, the manufacturing method reported in this study is a testament to the potential to innovate and improve the production of CAR T cell therapies for the benefit of more patients.”
In animal models, the researchers learned that the quality, rather than the quantity, of the CAR T cell product is an important determinant of their efficacy. Their experiment provided evidence that a smaller number of high-quality CAR T cells that are generated without extensive expansion outside the body is superior to a higher number of reduced-quality CAR T cells that are extensively expanded before returning to the patient.
Traditional manufacturing approaches require T cells to be activated in a way that induces the cells to replicate and expand in number. However, Penn researchers’ were able to remove this step of the manufacturing process using engineering approaches that built in part upon knowledge of how HIV naturally infects T cells, the team developed a way to deliver genes directly to non-activated T cells freshly isolated from the blood. This had a dual benefit of expediting the overall manufacturing process while also maintaining T cell potency. Patients cannot be infected with HIV through this process.
One of the limiters of cell therapies is patient access due to affordability, the researchers hope that by reducing the cost and time associated with manufacture these treatments could be made more cost-effective and therefore allow greater access to patients.
“This innovative approach is remarkable in that it may be able to help patients who might otherwise not be able to benefit from CAR T cell therapy, such as those with rapidly progressing cancer due to significant time currently need to generate these therapies,” commented the other co-leader of the research, Dr Saba Ghassemi, a research assistant professor of Pathology and Laboratory Medicine. “Efficient reprogramming of T cells with a CAR in as little as 24 hours in a more simplified manufacturing process without T cell activation or extensive culture outside the body also offers the possibility of expanding where and when these therapies are produced. Not only might it improve the production capacity of centralised manufacturing facilities, but if simple and consistent enough, it might be possible to produce these therapies locally near the patient, which could be tantamount to addressing the many logistical challenges that impede delivery of this effective therapy especially in resource-poor environments.”
The researchers concluded that their study “is a catalyst for more clinical research to investigate how the engineered CAR T cells, through this shortened approach, work in patients with specific cancers”.
Penn scientists led research, development and clinical trials of this pioneering CAR T therapy in collaboration with Novartis and the Children’s Hospital of Philadelphia. The University of Pennsylvania has licensed some technologies involved in these studies to Novartis.
Related topics
Anti-Cancer Therapeutics, Biologics, Biopharmaceuticals, Bioproduction, Drug Manufacturing, Immunotherapy, Preclinical Research, Research & Development (R&D), t-cells, Technology, Therapeutics