Fully instrumented 3D printed small-scale bioreactor developed
Posted: 22 November 2023 | Catherine Eckford (European Pharmaceutical Review) | No comments yet
To support upstream bioprocess development, a study has demonstrated real-time monitoring of the growth phase in a 3D printed, single-use bioreactor.
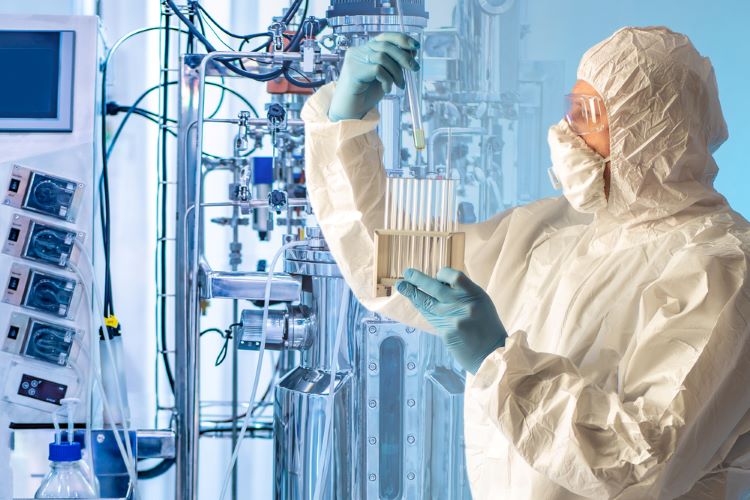
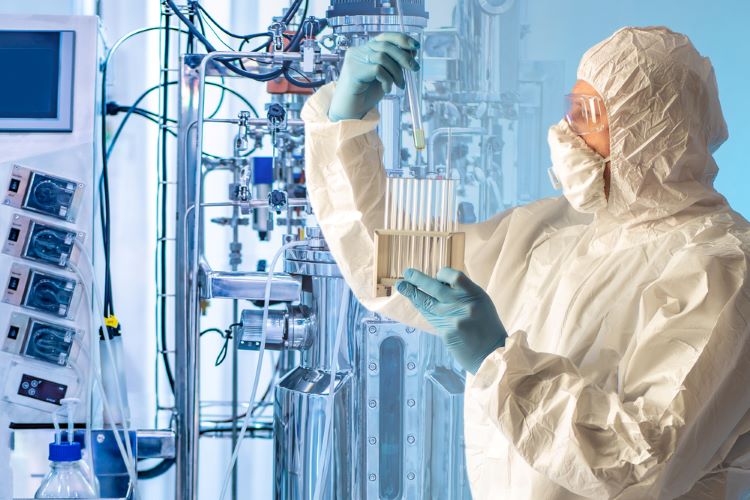
Researchers have reported on the development of a small-scale 3D printed, single-use bioreactor suitable for a broad range of mammalian and microbial cultivation. Overall, the study described in a paper published in Processes, illustrated the possibility of additive manufacturing of radiation-sterilisable, single-use bioreactors.
The paper explained that during upstream bioprocess development, small-scale instrumented bioreactors are required to investigate and optimise production processes in prior to large-scale manufacturing.
“Traditionally, the geometry of the bioreactor vessel has not been considered an easily changeable parameter. While custom building classical reusable bioreactors is possible, this is time consuming and can be financially prohibitive”, the researchers wrote.
Optimising a small-scale 3D printed bioreactor
Study method
The small-scale stirred tank bioreactor developed in this study was fully instrumented, with a working volume of 90 mL. Its integrated single use pH and DO sensors facilitated precise process monitoring and control, the authors stated, while the inline biomass sensor “proved to be applicable in both mammalian and microbial cultivations.”
Discussing the biomass sensor, the authors highlighted that a three-parameter fit enabled “the inline biomass measurements [to] be transformed to inline TCD and OD600 values. This transformation, showing satisfactory agreement with the corresponding offline measurements, enabled real-time monitoring of the growth phase.”
According to the paper, the presence of a levitating magnetic stirrer in the vessel enabled agitation at low filling levels and lowered the risk of contamination. This is because it did not require a penetrating stirrer shaft. Moreover, the absence of space on the headplate of the bioreactor allowed for probe ports and addition lines to be incorporated.
Findings and future developments
Positively, the findings from the study showed that there was “no indication of growth inhibitory substances leaching from the vessel material into the culture medium”.
Schneider et al. acknowledged a method to improve the effectiveness of the bioreactor in future experiments and later development: “increasing the system’s cooling capabilities which limited the E. coli process towards the end of the cultivation” would benefit the system’s performance.
Authors of the paper concluded: “To utilise the full potential of additive manufacturing in bioreactor manufacturing, the vessel geometry needs to be viewed as a parameter that can be optimised based on the needs of the experimenter, which is not restricted by the limitations of classical manufacturing technologies like injection moulding.”