Single-use systems for biotechnology products
Posted: 13 April 2017 | Scott R Rudge (RMC Pharmaceutical Solutions Inc) | No comments yet
Single-use systems have become an important tool in the development and scale up of biotechnology processes. Single-use systems save space, increase flexibility in scale and space planning and, to a large extent, eliminate cleaning costs in development and change over.
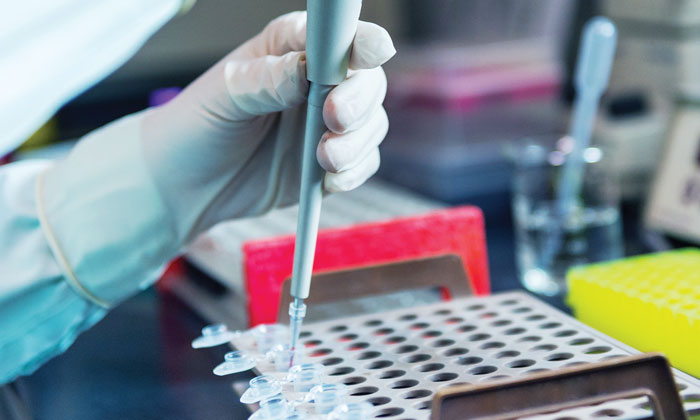
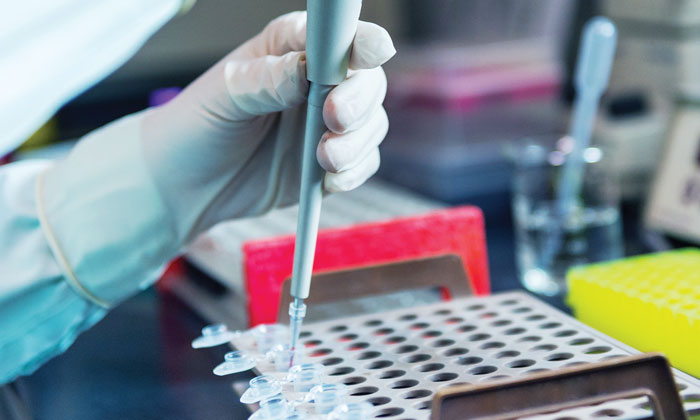
However, single-use systems come with their own challenges, including complete integration, scalability, and most of all with extractables and leachables. A comprehensive technical report has been published to guide potential new users through the process of implementing single-use technologies throughout their bioprocesses.1
Upstream processing has most fully embraced single-use technologies. From the thaw of the vial to the harvest of the bioreactor, it is possible to construct a fully disposable process stream for a cell culture process. However, limitations in heat and oxygen transfer have excluded bacterial and yeast processes. In this article, we review the available technologies and advances that have been made.
Vial thaw and cell expansion
The first steps of a cell culture biotechnology process are typically the thaw of a seed bank vial and the expansion of the cells in a series of shake flasks. In principle, these steps have always been performed in disposable containers, because the containers are small and cheap. However, there has been a change from glass shake flasks to plastic, since these are easier to transport. Since the materials are not as fragile, they can be gamma irradiated for sterilisation. This increases convenience, and increases sterility assurance, as gamma irradiation does not depend on the condensation of saturated steam in small material imperfections.
Although the materials may have changed in these steps, the footprint has not. Humidified CO2 incubator space and a sterile hood are still required. But it is possible to conduct the early stages of cell expansion without an autoclave, using all disposable, gamma-sterilised containers and implements. Eliminating the need for an autoclave also eliminates the requirement for high-quality water to produce clean steam. The utilities savings will be covered throughout this article.
Intermediate cell expansion
The intermediate steps of cell expansion are now dominated by disposable bags on rockers. This technology, pioneered by Wave, now owned by General Electric, relies on a tilting platform to mix the contents of the bag and transfer heat and oxygen. Expansion bags are largely differentiated by their materials of contact and a mixing pattern that is etched into their bases that affect the mixing pattern. These systems seem optimal up to a 20-litre total volume, 10-litre working volume, although they are available up to 1,000L total, 500L working. They have been proposed as production bioreactors, but they are not generally constructed to accommodate feeds, off-gas analysis and other features of high cell density high productivity bioreactors.
Intermediate cell expansion bags are generally easy to use and manipulate. They come pre-sterilised by gamma irradiation and do not require an autoclave. Sterile media is introduced directly through use of a sterile tubing welder, eliminating the need for an aseptic connection or a filtration step. Cells are also introduced through a tubing welder connection. Temperature and pH are monitored through integrated disposable probes, but dissolved oxygen is not typically measured.
There has been some concern with the polymer films used in cell expansion bags, as well as single-use bioreactors. In one often cited study,2 a chemical found at low levels in extraction studies was found to inhibit the growth of CHO cells when introduced at much higher concentrations. These findings have not translated consistently into manufacturing difficulties. However, research into biocompatible films continues.3
Production bioreactors
Production bioreactors are available as single-use unit operations up to 2,000L working volume. These systems are in wide use, primarily in facilities built within the last 10 years. Single-use bioreactors seem limited currently to about 2,000L, but it is not clear if this is due to limitations of the technology, or limitations of the benefits of singleuse systems above that volume.
Single-use bioreactors have largely been enabled by advances in antibody expression technology. Several companies claim antibody titers in excess of 10g/L with their proprietary expression systems, which are a combination of strategic placement of recombinant genes and high cell densities. When expression reaches 10g/L, a single 2,000L single-use bioreactor can produce 20kg of bulk antibody. This is sufficient for most antibodies, at least during clinical testing. If the product is approved for marketing, a larger scale may be justified, and the commercial product will typically be produced in stainless steel reactors.
There are some significant limitations to single-use bioreactors. Single-use bioreactors require fully hydrated media in order to reap the benefits of single-use systems from a utilities point of view. If dry media is purchased, it must be rehydrated with at least purified water, which requires both the utility, and a disposable media preparation system with cooling. Purchasing hydrated media at scales of 2,000L and above involves shipping large quantities of water, and large cooled storage spaces (or very well-timed purchasing). Logistics don’t always support ‘just in time’ supply of media, because many media are customised for products, especially feeds. If a base medium is purchased and supplements added on site, a source of high quality water is then required, although in this case the water may also be purchased. The stability of some media components in water is low, particularly glutamine.
Single-use bioreactors become very heavy at 500L scale and above. In many cases, a small crane is required to lift the bioreactor into its structure. In some cases, a fabric or polymer holder is placed inside the structure and the bioreactor is placed inside this structure. The bioreactor is inflated and properly rotated to place probe and sampling locations, and then media is introduced. These operations, and the subsequent dismantling of the bioreactor at the end of the process, can be as laborious and time consuming as cleaning in place. However, the utility is not required, so some savings are realised.
Single-use bioreactors require significant structural support. The support not only holds the side walls of the bioreactor, but also provides some temperature control, and support for instruments and sampling ports. The support is not as expensive as a stainless steel bioreactor, but it is as specific, in that a 1,000L bioreactor will not fit in a 2,000L structure. In this aspect, flexibility and footprint are nearly equivalent to installed stainless steel bioreactors.
Media preparation
It is the goal of single-use technologies to reduce utility requirements, the most prominent of which are a distilled water (water for injection) system, a steam sterilisation system, and a clean-in-place system. When the choice of single-use technologies is made for upstream processing, any choice that requires the installation of any of these systems defeats the major advantage of the single-use technologies. The most significant consumer of these clean utilities is media preparation, which consumes a significant amount of water, and requires sterilised containers in which to make media. For this reason, many companies now outsource their media preparation, and have it delivered in single-use containers. Most media suppliers now offer this service, and will formulate a customised base media and feed solutions that have been optimised for the particular culture and product. This has cut down considerably on facility costs, but added a logistical cost to manufacturing.
Single-use bioreactors require fully hydrated media in order to reap the benefits of single-use systems from a utilities point of view
The downside of outsourced media preparation is the stability of the media and its handling and ordering. Cell culture media (as mentioned above, total single-use solutions are not yet available for large-scale bacterial cultures) has multiple components of varying aqueous stability. Detailed studies of the stability of each ingredient in cell culture media is prohibitive, and rarely explored, leaving the highly subjective and imprecise ‘use test’ as the best way to determine the stability of the medium as a whole.
For a 2,000L culture, typically at least 1,000L of base media will be required, which, being a metric ton, requires significant equipment to move it through the facility. Typically, the bioreactor is in an ISO Class 8 or better environment, which is not truly compatible with the types of equipment required to move 1,000L of media. Of course, smaller lots are often ordered, which increases the complexity of filling the bioreactor, and increases the number of connections that must be made. Additionally, since the media must move through the facility, frequently the single-use container is custom designed to fit through doors and attach easily to the bioreactor. The custom design of single-use containers, which involves drawings approval, user requirement specifications and, in some organisations, validation, adds to the cost and lead time for single-use systems.4
Finally, stability, shipping and storage requirements are issues. Since stability of the media is difficult to know precisely, as previously described, organisations are conservative. They set short ‘use by’ dates because the cost of using expired or spoiled media in a batch in terms of lost time in plant are very high. Additionally, providing cold storage for large volumes of media increases the footprint. If cold storage is not available, the room temperature storage time of media is even shorter, decreasing flexibility. The heat load presented by 1,000kg of waterbased media is also considerable, so if cold storage and cold shipping are required, expect to pay dearly for the required refrigeration tonnage. Finally, the outsourced media preparation service is a popular one, and back orders and lead times can be long. When a facility is built without the capability to reconstitute media, very few alternatives exist in a crunch.
Enabling technologies
Single-use technologies have been widely adopted in cell culture based manufacturing, especially with CHO cells. However, the technology has been greatly aided by the development of other technologies, which have been mentioned above. The primary enabling technologies have been the laboratory-based tubing welder, high titer CHO expression systems and increasingly widespread availability of gamma irradiation sterilisation. Without these additional technologies, it would not have been possible to displace a more traditional fixed plant or stainless steel approach to producing complex glycosylated biomolecules.
Many mammalian cell culture manufacturing facilities are now converted to single-use upstream platforms, and economic analyses suggest that these are the most economical, especially in a multi-use facility, where change-over costs between products are also significant in multi-use equipment.
Downstream applications
Downstream applications for single-use technologies are in some cases more mature, and in other cases not yet truly available. Filter capsules have been available for many decades now, and before those were available, filter cartridges covered most applications, although they required a housing that was multi use. Replacement of buffer tanks with buffer bags has become prevalent and will be discussed below. Chromatography is the most notable unit operation that has not yet become truly single use in a widely applied platform.
Cell harvest
Mammalian cell harvest by centrifuge has been largely displaced by depth filtration. Depth filtration uses single use plastic pods that have no reusable wetted parts. These depth filter pods are held in a vice-like holder because the plastic housings themselves do not have the pressure capacity required. Depth filtration is an adequate, although somewhat expensive, alternative to centrifugation. As with other disposable technologies, depth filtration reduces installed costs in a facility but increase operating cost per batch.
Chromatography
Chromatography unit operations have been adapted to single-use technologies, with the exception of the resin and the column itself. Buffers, which will be addressed below, are prepared and stored in single-use bags that are wheeled around in open-top carboys. The flow path through the chromatography control skid is available as a single use flow path in the Äkta Ready. This single-use flow path threads through a free standing Äkta control system, which uses pinch valves for flow regulation. The flow path includes a disposable air trap, sensors, flow cells and peristaltic pump tubing all integrated into two pieces – a pre-column piece and a post-column piece. The Äkta Ready can be used with pre-packed columns or with traditional chromatography columns. This application of disposable technology is effective but not cheap. However, the price should come down as competitors enter the market, volumes increase and the technology matures.
Chromatography columns are available in a single-use format, but there has been no fundamental change to the technology to adapt it to single use. The same resins that are packed into reusable columns, at the same price, are packed into a plastic cartridge and sealed. These columns can be used once, or multiple times, depending on the requirements of the process. However, most resins are too expensive to consider using them for just one batch, even if the resin volume is reduced by performing multiple cycles. Until the cost of resin is reduced, chromatography columns cannot be considered single use. However, there is an emerging competitor to fixed bed chromatography that has a cost more appropriate to single use, discussed in the following section.
Membrane chromatography
Membrane chromatography is advancing as a downstream purification technology.5,6 Membrane material can be derivatised with many of the same ligands as are used in conventional chromatography, and proteins and impurities bind to and release from these ligands in much the same way. However, kinetics are much improved, as there is convection in the pores of the membrane and no pore diffusion into and out of the resin particle. The disadvantages to membrane chromatography are that resolution is low, due to mechanical design of filtration devices, and ligand binding density is low relative to fixed bed chromatography. For these two reasons, most applications of membrane chromatography are ‘flow through’, in which only impurities are bound to the membrane, and the target product flows through.
This is good for second and third steps in a purification process where the product is enriched relative to impurities, but not a great solution for the capture step, where the product is isolated from a pool of contaminants in much higher concentration. Although there is no theoretical limit to the ligands that can be attached to membrane materials in use for membrane chromatography, the most widely used membranes are based on ion exchange. Hydrophobic interaction and affinity modes are used in membrane chromatography much less frequently.
Filtration
Filtration applications, as mentioned earlier, have been available in single-use formats for decades. There have not been significant advances in this technology. Ultrafiltration and microfiltration modules are more commonly available in plastic housings, but like fixed-bed chromatography, the cost of not reusing such modules is high. Advances in membrane material cost are needed to make these units reusable in an economic sense.
Reactions
Reactions in downstream process, such as enzyme activation and conjugation, are perfectly adaptable to single-use technology in the form of bags set in temperature controlled jackets. Mixing is performed through a magnetic drive motor and magnetic mixer. Single-use technologies have not been adapted to reactions requiring vacuum or pressure. Organic solvents that might be required should be used with caution after checking the extractables spectrum for that solvent. In general, available data on extractables for single-use materials in organic solvents is limited, primarily to alcohols.
Buffers and buffer preparation
Single-use technologies are well adapted for the preparation and storage of aqueous buffers. Most buffers for protein purification are between pH 4 and 8, are prepared and stored at room temperature or cold, and are used in fairly small quantities. Buffers can be prepared in mixing bags as previously described, however it is generally desirable to use cooled water rather than 80°C water for injection. Cooling buffers in single-use bags in situ is generally more difficult than the same operation in stainless steel because the thermal conductivity properties of plastics are less, and the surface contact between the outer jacket and the bag is not always uniform. Also, the films used in single-use containers are not always stable to high temperatures. Once a buffer is prepared, it can be filtered into a storage bag. Frequently, these are tank liners that are open at the top, but they can also be sealed to provide bioburden protection.
Extractables and leachables
The major issue for single-use technologies is the potential for chemicals from the polymer process to diffuse into the product or buffer stored in the disposable container. These chemicals can be unreacted monomer or dimer from the polymerisation process, plasticisers or other chemicals used to affect the properties of the final material, releasing agents and lubricants that are used in the moulding process, and degradation products from storage, transport and gamma irradiation. These chemicals are frequently reactive on their own, so may interact with the protein product in undesirable ways, or have a toxicity profile not compatible with the intended use of the protein product.
Measuring these chemicals usually requires different analytical techniques to those commonly used for protein products.7 Since the amount and properties of the potential chemical contaminant are unknown, an analytical method that can detect a wide range of chemicals is required. Finally, the presence of a high concentration of protein, quite often one or more organic buffers, and a surfactant, makes detection and quantitation of small levels of polymer-related chemicals very difficult. Therefore, model solvents are often used, to simulate the pH, temperature and osmotic pressure of the substance that will be in contact with the single-use material. When a chemical is found in a model solvent, it’s called an ‘extractable’.
When it is found in the actual pharmaceutical product, it is called a ‘leachable’. The US Pharmacopeial Convention (USP) has adopted a General Information chapter, <1663>, addressing the testing to consider when plastic containers are used in pharmaceutical processing.
Extractable and leachable testing is a source of risk for pharmaceutical processing. Understanding this requires careful risk analysis and management, and the generation of significant amounts of data. The cost of extractables and leachables testing should be considered when opting for a single-use manufacturing platform.
Single-use systems are still under development for downstream protein purification, primarily chromatography resins and ultrafiltration membranes. When these become cost effective to use once and throw away, downstream processing will truly be single use. Other elements of downstream processing have been using single-use technologies for many decades. Extractables and leachables are a bigger concern downstream, as the product is closer to the patient.
Drug substance storage
One of the earliest applications of single-use technology was drug substance storage. Bags resembling IV drip bags were commercially available in the late 1980s. These bags could be frozen, shipped, and thawed at the site of drug product manufacture. However, it was found that the plastics used were brittle when frozen and the ice formed sharp edges which could slice the bag open by shifting. So, protective cases and trays have been designed for the bags, and controlled-rate freezing and thawing skids have also been built.
Drug product applications
Drug product manufacturing for cell culture derived proteins typically involves the filling of prefilled syringes, cartridges or vials in an aseptic environment. Single-use tubing is available to transfer formulated drug solution to the final container.8 However, the non-plastic parts of a drug product manufacturing flow path are generally limited to fill needles and sometimes pumps, which are easily dedicated to a product and cleaned out of place. Additionally, operating a drug product manufacturing facility without the benefit of water for injection and clean steam is, so far, somewhat beyond reach. So, although single-use technologies are used in drug product manufacturing, complete reliance on disposables is still rare in drug product manufacturing facilities.
Conclusions
Single-use technologies have made significant progress in the last decade, and it is not feasible to consider operating a manufacturing facility without a water for injection system, a clean steam system and a clean in place system. Upstream single-use technology is advanced and has enabled the production of cell culture based proteins at the 2,000L scale, which combined with high titer expression systems, enables production on the 10kg/batch scale. Downstream protein purification can also be run with an exclusively single-use platform, but the costs of resins and ultrafiltration membranes are still somewhat prohibitive. Single-use technologies have advanced rapidly and are generally cost competitive with completely installed technologies.
About the author
References
- Technical Report No. 66. Application of Single-Use Systems in Pharmaceutical Manufacturing. Parenteral Drug Association. 2014.
- Hammond M et al. Identification of a leachable compound detrimental to cell growth in single-use bioprocess containers. PDA Journal of Pharma. Sci. and Technol. 2013;67:123-134.
- www.interphex.com/en/Sessions/35238/Fortem-Challenges-and-opportunities-indeveloping-a-new-plastic-film-for-bioprocess-activities.
- Gonzalez MM. Disposables – critical design considerations. American Pharma. Rev. July 2011:78-85.
- Zhou JX, Tressel T, Guhan S. Disposable chromatography. BioPharm. Intl. 2007;20(10):25-33.
- Lim JAC, Sinclair A, Hirai M, Gottschalk U. Disposable membrane chromatography – counting the cost. BioPharm. Intl. 2007;20(10):34-20.
- USP 39-NF 34 General Chapter <1664>.
- Leveen L. Presterilized, single use filling systems for liquid bio-pharmaceuticals. American Pharma. Rev. August 2010;30-33.