Maintaining pharmaceutical operations during a pandemic through innovation and remote technologies
Posted: 12 November 2020 | G Balaji (ABB India), Ravi Kalla (Anthem Biosciences) | No comments yet
G Balaji and Ravi Kalla explains how Pharma 4.0 can be implemented at a CRO to enable work to continue even during a global pandemic.
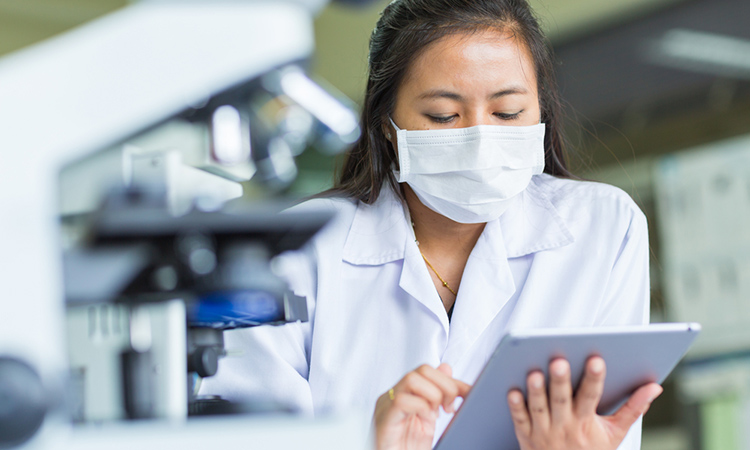
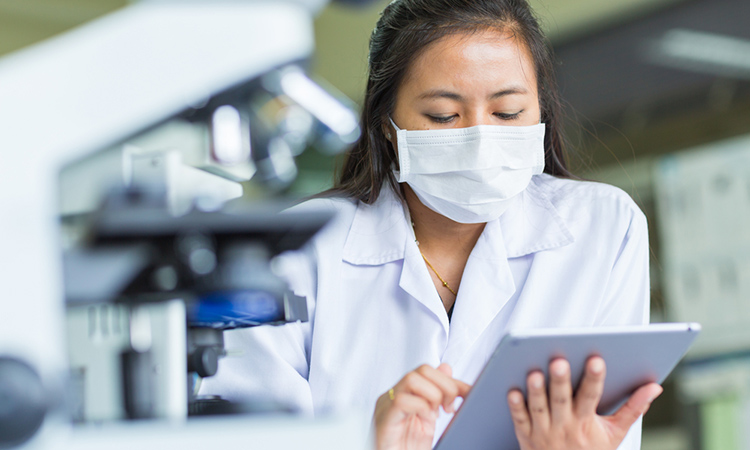
In India, a unique, collaborative project is challenging conventional thinking on how pharma companies can approach the convergence of IT and process automation technologies (OT) layers for remote operations and mobile solutions.
Installing an integrated system that combines active pharmaceutical ingredients (API), fermentation, biologics and building management systems, continuous monitoring systems and environmental monitoring systems at its 15-acre pharmaceutical campus in Bangalore, has enabled Anthem Bioscience, a contract research organisation (CRO), to improve efficiency, high availability and accessibility of production systems during the recent pandemic – with only a fraction of its workforce working onsite.
This is particularly relevant in light of the COVID-19 pandemic and the resultant worldwide lockdowns. The pharma industry is an essential service at the forefront of the battle to find a vaccine against the novel coronavirus. It is imperative to develop and distribute a vaccine while maintaining an uninterrupted supply of other medicines to the public.
Pharma is one of the most heavily regulated industrial sectors. With the onus on companies to validate internal systems and protocols as per US Food and Drug Administration (FDA) and other regulatory bodies’ standards while fully complying with 21 CFR Part-11, ISA-88 and GAMP V, digital solutions can help ensure end products consistently satisfy international standards.
Addressing pharma workflow inefficiencies
This not only streamlines regulatory compliance, it gives personnel unprecedented visibility along the entire production value chain and enables real-time monitoring of assets using human machine interfaces for informed decision-making, while working on fixed terminals, remotely on tablets or mobile phones.
Manufacturing equipment including process equipment (upstream and downstream), clean and other utilities such as reactors, dryers, hydrogenators, nutrient dosing, media preparation, buffer vessels, fermenters, bio-reactors, thin film freezing (TFF), chromatography systems, lyophilisers, process water, plant steam generation and distribution systems and solvent distribution systems are typically purchased from multiple original equipment manufacturers (OEMs), meaning multiple programmable logic controllers (PLCs) and supervisory control and data acquisition (SCADA) systems – each with their own graphics, presentation and logics elements – are scattered throughout the plant in individual silos that operate simultaneously.
This results in more complex operations, integrations, customisation, maintenance, manpower, training, qualification, lack of high availability and business continuity and more dependence on OEMs/vendors, which makes it difficult for personnel to operate efficiently and get actionable data in and out of machines in a timely manner that can be used in a consistent way.
Anthem has maintained safe, efficient operations during the pandemic lockdown”
Multiple hardware, network, storage and back-up systems associated with numerous PLCs also cost more than four to ten times, depending on the complexities in terms of operating expenditure (OPEX), than employing a centralised system and business continuity and high availability is always a concern. For example, in a typical PLC environment, in case of a failure, either the PLC/SCADA systems needs to be fixed or replaced and re-qualified as per good manufacturing practice (GMP) standards. This may take around three to 15 working days, depending on various constraints. Losing the equipment – and thus experiencing downtime – for such a long period may result in a significant loss in terms of deliverables and revenues.
Integrated DCS and secure data centres
To address these issues Anthem and ABB, along with the pharma equipment vendors, built logics, graphics and IT infrastructure and unified it in a single platform for ease of use. Chemical API, biological and formulation manufacturing and the building management system are all integrated. Monitoring and control of these critical systems are from ABB Ability System 800xA Distributed Control System (DCS) from two data centres at the Bangalore site.
Multiple data points relating to everything from humidity and temperature control and pure steam systems to differential pressure in classified and unclassified areas is all part of the centralised DCS.
ABB management software gives key personnel access to this data at every stage of the production process – from material storage to manufacturing and dispatch – to facilitate analysis, reporting, production planning and quality and asset management.
Having these elements in one unified system, that delivers real-time visibility of entire processes to business users across the plants, which is tightly integrated with the IT infrastructure, has had a significant impact on reducing time and cost. This solution enabled the workforce to operate remotely and monitor the critical processes during the pandemic. It also helped the CRO optimise the capital expenditure (CAPEX) and OPEX investments, increased availability and business continuity and reduced dependence on vendors significantly.
The benefits of virtualised architecture
The DCS architecture including server, storage and application software like SCADA/human-machine interfaces (HMIs) are virtualised. Using HMIs on tablets and smartphones, Anthem has maintained safe, efficient operations during the pandemic lockdown with just 10 percent of its IT and automation team and 25 percent of its process team on site.
Adoption of such technologies is set to continue in the pharmaceutical industry”
One of the unique capabilities of ABB Ability™ System 800xA is that it is not filtered or selective data. The virtualised architecture allows staff to access the same screen as the plant operator in the control room – with identical granularity and in near real time – on a tablet or mobile device.
This means staff are able to monitor key parameters at the Bangalore facility from their own homes, reducing the cycle time needed to analyse any potential issues and take corrective action.
By employing remote-enabled solutions and integrating plant operations into a single localised DCS, Anthem also realised CAPEX savings of up to $9,000 per piece of equipment, compared with buying multiple PLCs. Associated licence, hardware and maintenance costs were also significantly reduced.
In addition, the virtual architecture has enabled Anthem to reduce manpower in several business verticals and because the project converges IT and OT, the CRO has invested heavily in cybersecurity.
Further adoption of Pharma 4.0
The project began in 2016 with ABB’s delivery of a chemical synthesis and fermentation solution in the chemical plant. This was followed in 2017 by an expansion of the fermentation system. The concept of a common integrated building management system (BMS) was developed in 2016 and last year ABB delivered a unified distributed DCS and BMS for the additional biologics manufacturing plant at Anthem’s manufacturing campus in Bangalore.
Four years on, Anthem made its plant operations available to its staff on either a tablet or mobile phone. A key element of this strategy is IT and OT integration, whereby staff have complete insight of factory operations, processes and real-time data while working remotely. This will enable the CRO’s future digital strategy of artificial intelligence (AI)/machine learning and predictive manufacturing processes.
Adoption of such technologies is set to continue in the pharmaceutical industry, particularly in the area of predictive manufacturing. In addition, being able to retrieve data easily and quickly in this way also makes auditing easier and helps bring lucrative products to market more swiftly.
The unprecedented challenge presented by the COVID-19 pandemic provides a huge opportunity for businesses within the pharma industry to continue to challenge existing business practices and identify areas for innovation, using automated and digital solutions.
About the authors
Related topics
Contract Research Organisations (CROs), Lab Equipment, Outsourcing, Technology
Related organisations
ABB, Anthem Bioscience, US Food and Drug Administration (FDA)