How thermal fluid maintenance maximises productivity
Posted: 11 July 2017 | Clive Jones | Global Heat Transfer | No comments yet
Global Heat Transfer’s MD, Clive Jones, gives 3 considerations for manufacturers operating thermal fluid heat transfer systems to safeguard the system’s future for the long term.
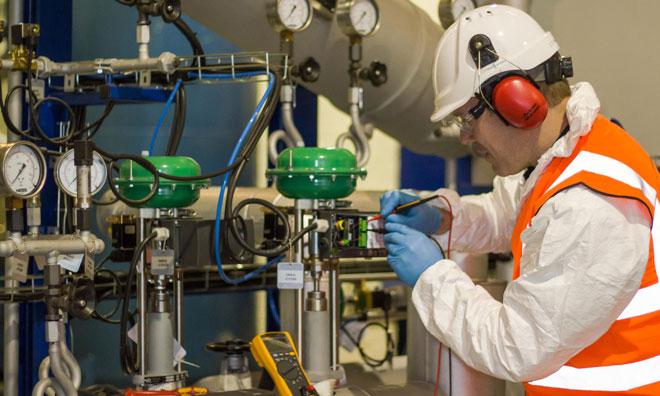
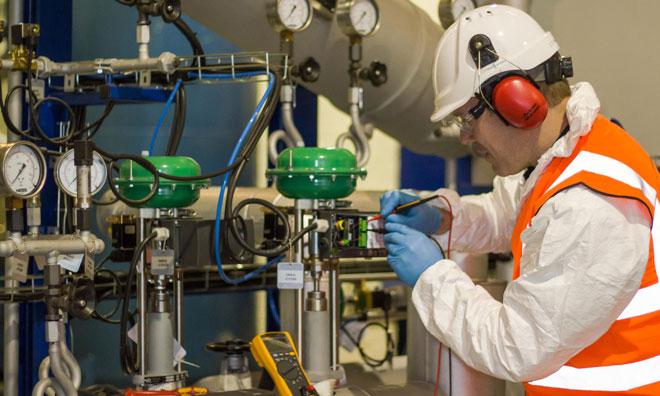
The Oxford Electric Bell has been ringing constantly for over 175 years – so much so, that the apparatus has been dubbed the world’s most durable battery. But after all this time, it is still a scientific mystery how the bell has functioned for so long.
For operators of thermal fluid systems, keeping operations running doesn’t have to be a mystery. Here, Clive Jones, managing director of heat transfer fluid specialists, Global Heat Transfer, gives three considerations for manufacturers operating thermal fluid heat transfer systems to safeguard the system’s future for the long term.
In chemical processes that require indirect heat, there are two methods that dominate the industry — steam and thermal fluids. To achieve high operating temperatures, steam requires extremely high pressure and an intensive continuous maintenance programme. In contrast, thermal fluid systems offer increased safety, flexibility and efficiency with the added bonus of a maintenance programme that is significantly less intense.
Because of their benefits, thermal fluids are used in many industries including pharmaceutical or food and beverage processing, chemical and industrial manufacturing. Although thermal fluids don’t require the level of assessment of steam systems, there are still factors the operator needs to be aware of to keep the system safe and efficient. Here, we explore three ways to increase system life span, maximise productivity and reduce the risk of costly downtime.
Know the legislation
There is a body of health and safety legislation that companies must follow to ensure a safe working environment, particularly when working with flammable materials. The system operator should have a detailed understanding of the legislation that applies to thermal fluids — the Dangerous Substances and Explosive Atmospheres (DSEAR) regulations and the Explosive Atmosphere Directive (ATEX 137). Staff training can help make sure that employees are aware of what is necessary for compliance.
Not all manufacturers are aware that thermal fluids can degrade if they are left neglected for long periods of time. The degradation processes of oxidation and cracking can produce by-products that increase the risks associated with the system, so it is important the operators prioritise their maintenance regime.
Be ahead of the curve
Oxidation and cracking can lead to safety risks if light ends are produced and reduce the flash point of the fluid. Further degradation can lead to carbon build up in the pipes which reduces system efficiency. If these problems are addressed early, they can be tackled with a simple diluting process or other interventions, rather than a more time consuming and expensive full clean and flush. It is therefore in the best interests of the manufacturer to stay on top of thermal fluid condition from day one, with proactive maintenance that happens before anything has had a chance to go wrong.
Stay on the ball
The plant manager should also ensure that the facility always has members of staff available on site that have been trained in thermal fluid management and thermal fluid systems. Employees should be trained on thermal fluid maintenance, general housekeeping, storage, safe handling and how to survey a system. It may also be helpful to make them aware of the insurance and legal obligations.
The best way to manage thermal fluid condition is to incorporate a proactive maintenance programme that encompasses regular thermal fluid sampling and analysis, training and engineering support, such as Global Heat Transfer’s Thermocare. Having a comprehensive programme in place can give the manufacturer peace of mind, and a better understanding of how to safeguard their system, removing the mystery of how to minimise downtime.