Current trends in freeze-drying
Posted: 21 August 2017 | Yves Mayeresse | No comments yet
This article reviews the trends in freeze drying highlighted at recent Parenteral Drug Association (PDA) conferences…
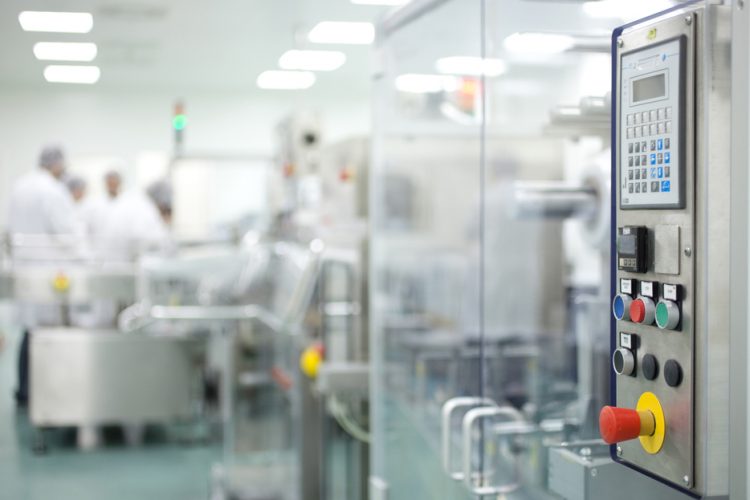
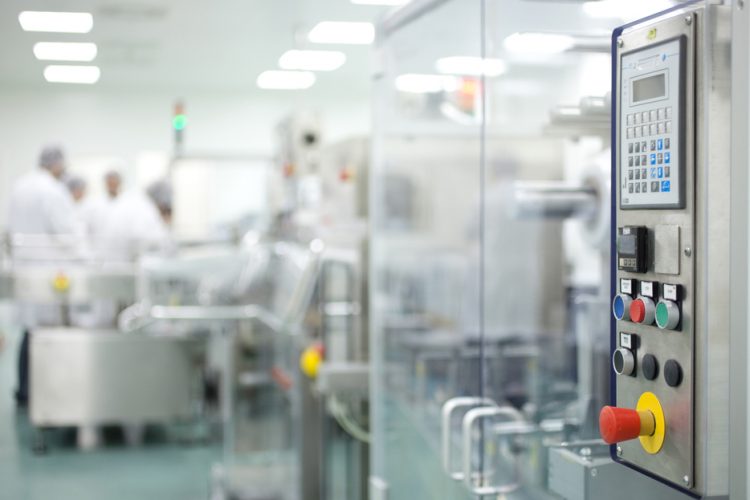
Controlled nucleation is one of the most topical trends in the industry, as the freezing step is of paramount importance for stability of products. The temperature range between 0°C and the real crystallisation temperature is called supercooling, spanning over 10°C in a freeze-dryer. Unfortunately, the lack of control of nucleation temperature can affect product uniformity and lead to suboptimal freeze-drying cycles.
Controlled nucleation technology allows for a significant decrease in the nucleation temperature variability. Different technical solutions are available; one is the ice fog technology, which consists of introducing small water crystals into the chamber. Another example is a method that creates an important pressure difference inside the freeze-dryer through a carefully timed depressurisation event. The question for the pharmaceutical industry relates to the advantage of controlled nucleation in terms of product stability compared to a more classical, well-established freezing protocol. The product data have now started to emerge and some of them will be reviewed during this edition of the PDA conference.
Process analytical technology (PAT) has been supported by authorities for more than 10 years. New analytical devices can now be added to freeze-dryers. Mass spectrometers can be adapted to check for absence of silicone oil. These devices are also used to analyse the different gas concentrations during freeze-drying cycles, allowing precise end-point determination of primary drying. This helps to assess reproducibility between cycles and during cycle development.
The Pirani probe, a pressure gauge using a hot wire system, is sensitive to different gases. This probe is used in combination with a capacitance diaphragm vacuum gauge, measuring the whole quantity of gases in the freeze-drying chamber. The system is also able to determine the end-point of primary drying. This kind of gauge has existed for years, but its recent capacity to sustain sterilisation allows it to become a PAT tool on industrial freeze-dryers.
The best outsiders in this category are the product temperature probes; they were commonly used in the past to monitor product temperature inside the vials, a critical product parameter for freeze-drying cycle monitoring. However, with automatic loading and unloading of freeze-dryers, those probes could not be used anymore, creating a gap in the usually monitored parameters. Nowadays, wireless probes are commonly used to measure real-time temperatures in some vials through an antenna system (inside the chamber). The values are used in mathematical models to compute vial heat transfer coefficient (Kv) as a function of chamber pressure. However, the major concern remains to enter those probes inside an isolator or closed RABS, but potential solutions are emerging.
Design of experiments
Mathematical models and design of experiments (DOE) are now commonly used for the development of freeze-drying cycles. Interesting discussions arise between believers in a full theoretical approach and the inference of specific models issued from small-scale trials. The theoretical approaches are increasingly refined and some of them are valuable for predicting different events encountered during a freeze-drying cycle. They allow simulation to find ideal conditions for the developed process. Moreover, DOEs allow the boundary conditions of a specific process to be defined. In terms of validation, this approach makes more robust the set of data that can be supportive for the filing of a new product using critical process parameters (CPP) of the freeze-drying cycle and their related impact on the quality attributes (QA) such as the potency or residual moisture for the product.
Evolution towards a continuous process is one of the objectives for primary operations. A more continuous process from fermentation up to formulation is described in different presentations. Currently, freeze-drying remains a traditional batch-to-batch process. Nevertheless, in the food industry continuous freeze-drying is widely known and has been used for decades. However, the pressure applied in the chamber and the aseptic level is of course different to the requirements in the pharmaceutical area. Over the years attempts have been made to apply the concept to increase yield, decrease cost of goods sold, and be more flexible. Recently, different initiatives have taken advantage of new developed technologies and PAT.
Finally, subjects such as new excipients used for formulation design and molecule stabilisation, are still present but less studied. Automatic loading and unloading of freeze-dryers evolved from the status of new technology to a standard in the industry. There is still potential for equipment evolution in terms of performance increase, weight decrease, and reduced energy consumption.
In conclusion, freeze-drying is still an evolving technology that follows the trend of the pharmaceutical industry with potential breakthroughs for the design of future factories.
BIOGRAPHY
Yves Mayeresse is Director, Manufacturing, Science and Technology (MSAT), GSK, Wavre, Belgium. He is a member of the Parenteral Drug Association (PDA) and chairman of the PDA conference on freeze-drying. The content of this article is not influenced by the PDA in any way, although the association is cited in the text.
The PDA is holding a conference on Pharmaceutical Freeze-Drying Technology on September 19-20 in Cologne, Germany.
For more information about the PDA Freeze Drying Conference, please check the website www.pda.org.