How tablet formulation can impact production
Posted: 3 September 2019 | Rob Blanchard (I Holland) | No comments yet
Transforming a formulation into a successful solid dose product is a complex process that involves many considerations. Given the ever-growing demand for increased tablet quantities and the goal of reducing time to market, Rob Blanchard explains how the pressure is on manufacturers to find innovative processes to improve production efficiency.
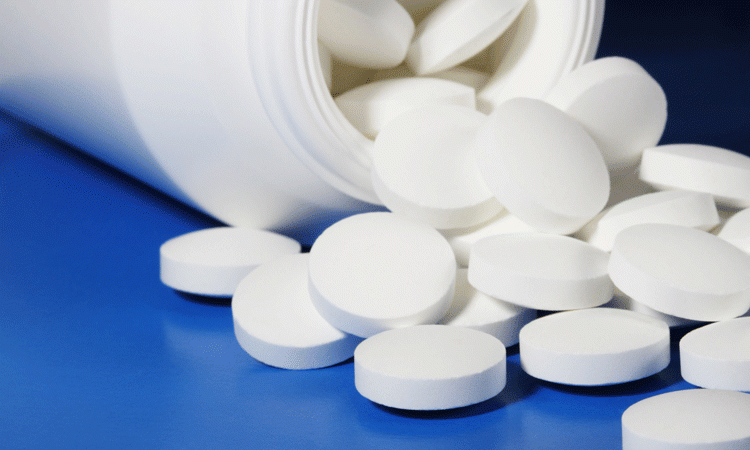
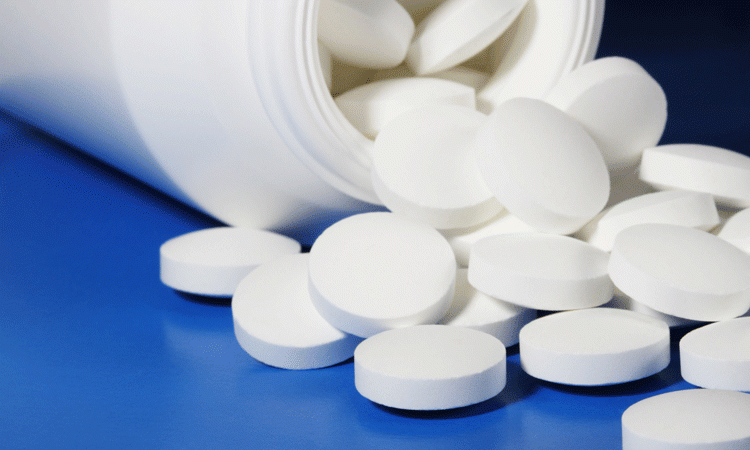
WITH THE GLOBAL oral solid dosage pharmaceutical formulation market forecast to grow from $493.2 billion in 2017 to $926.3 billion by 2027, representing a value CAGR of 6.5 percent over the forecast period, getting production right in the early stages is crucial to prevent expensive faults and tablet defects in the downstream production process.
When we look at the compression process, the physical content of the formulation adds a significant layer of complexity to producing a quality tablet, with factors like moisture content, abrasiveness and particle size affecting its compressibility. The overall formulation composition must be examined to enable application of the correct tooling specification to suit the product being compressed. Punches and dies must be selected according to the characteristics of the formulation and the correct tooling maintenance and standard operating procedures (SOPs) should be followed in order to reduce or mitigate the impact of the many variables affecting tablet manufacture.
Moisture – a root cause of sticking
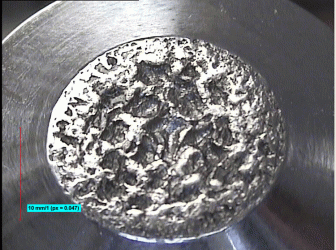
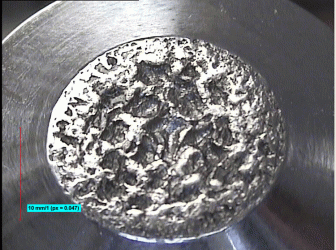
Figure 1: Wear to the punch head.
Pharmaceutical formulations will contain ingredients with differing levels of moisture content. Generally speaking, this is required to help bind the ingredients into a viable robust solid dose form. Although some degree of moisture is important, it can also negatively affect the tablet as it can lead to sticking. Sticking is when material adheres to the surface of the punch tip face or die bores. This build-up of granule results in tablet defects and has a detrimental effect on the appearance of the finished product. Simply put, sticking occurs when the adhesive forces of the formulation to the punch tips overcome the cohesive forces within the tablet.
Moisture within the tablet can be a root cause of increased adhesive force. This happens when there is an increase in capillary action between the tooling surface and the granule. Capillary bridges form, causing high adhesion areas, which results in sticking. It is worth highlighting that it is not just moisture within the formulation itself that can be problematic; moisture can also enter the production process through the environment in which the tablet is compressed. Excess humidity in the compression room or areas where the formulation is stored prior to compaction can also negatively affect how the formulation adheres to the punch tips.
One solution to sticking caused by high moisture content is to apply an anti-stick coating to the tablet tooling to repel, rather than attract, moisture from the steel. The finish of tooling is an important factor in overall performance and consequently the sticking potential. Coating technology has advanced considerably over the years and, when used in conjunction with high-quality tooling steel, tool coatings are increasingly becoming an acceptable means of solving production problems, such as sticking. They enable better tableting efficiency and output by reducing the requirement for tools to be taken out of production for additional cleaning and maintenance work to remove problematic residue.
Specialised services are available that use algorithmic predictive models to quickly calculate the best anti-stick coating for compression tooling based on the properties and characteristics of the formulation. When coatings are developed correctly and their beneficial characteristics are matched to those required by the formulation, they can help to prevent sticky formulations adhering to the punch tip faces and can be beneficial in increasing corrosion and wear resistance.
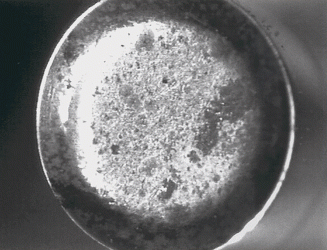
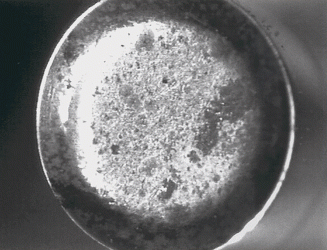
Figure 2: An example of corrosion.
Traditionally, the most popular coating used within the global tablet tooling industry is hard chromium, due to its low cost and general-purpose characteristics in terms of average anti-stick, anti‑corrosion and anti-wear properties.
This material, however, comes with several problems; for example, micro-cracking, which allows aggressive tablet formulas or cleaning solutions to attack the steel beneath the coating and hydrogen-embrittlement, which decreases the tool steel’s strength.
Superior alternatives have been developed to alleviate the problems commonly encountered with hard chromium. Tooling manufacturers have designed specialist coatings that enhance the performance of substrate material for punches and dies and prevent issues such as sticking.
Put a stop to aggressive formulations
Aggressive formulations can have adverse effects on tablet tooling; for example, some ingredients are particularly abrasive and comprise hard and sharp elements, which causes damage to the punch tips when under compression. Through repeated cyclic compression these abrasive ingredients can abrade both the surface of the punch tip and the bore of the die, resulting in low quality tablets.
Hard granules can even impregnate the surface of the punch tip under high compression forces. These actions can then lead to other tableting problems, such as capping or de-lamination and sticking. This abrasive action can be countered using advanced tooling materials and coatings selected for their wear-resistant properties.
Formulations containing corrosive elements such as chlorine, salts and acids will react with the tooling surfaces and result in oxidation”
Dies should always be made from steel that has superior wear resistance. Commonly used materials for tooling are generally based on high-carbon, high-chrome cold-work tool steels. However, when extended wear resistance is required, tungsten carbide is often used for the dies as it combines a high compressive strength with an extremely high wear resistance, which helps to reduce die bore wear, deformation, ringing and lasts longer than conventional die steels. Selecting a wear-resistant punch coating will also counter any abrasive formulation to make the tablet tooling more robust in order to withstand the rigours of compaction.
Tool steel consideration is also important to combat corrosive granules. Formulations containing corrosive elements such as chlorine, salts and acids will react with the tooling surfaces and result in oxidation. In addition, wash in place systems fitted to some modern tablet presses expose tooling to water and cleaning solutions, therefore necessitating that the tooling has good corrosion-resistant properties.
Post-compression cleaning procedures can also cause corrosion if not controlled appropriately. Corrosion can be detected by the appearance of discolouration, etching or common red rust. To prevent this issue a corrosion-resistant material can be selected. Specialised martensitic stainless steels with high chromium content should be used and it is also advisable to consider applying a coating with corrosion-resistant properties such as chromium nitride.
Small particles can lead to poor quality
Some formulations can contain very small particles, or fines, which affects the selection of appropriate clearance between the tip of the punch and the bore of the die.
To optimise tablet production and quickly produce mass robust tablets with tailor-made properties, every process must be considered, starting with the formulation”
If the clearance is too large, then the smallest fines of the formulation can pass between the punch and die. This can cause numerous problems including binding and tightness of the punch tip in the die bore, which will generate friction and heat, causing abrasion of both the die bore and the punch tip. This in turn results in die bore ringing and tip abrasion, causing flashing around the edge of the tablet.
Fine particles can also move through to the lower punch guide seals and if these are not sufficiently fitted or worn, further tightness and wear can be generated between the punch barrel and lower guides. Fines can also cause a general contamination issue as they are more easily airborne and can penetrate upper guides with similar results if seals and bellows are not used and maintained correctly.
Excessive fines can result in poor tablet quality, as well as tool binding and tablet press overheating, which can in turn increase sticking and picking issues.
Know your formulations’ characteristics
In cases of formulations involving more time-dependent consolidation behaviour, a long dwell time is important to create strong bonds between the particles. When particles are subjected to a compression force for a longer period of time, further plastic behaviour is demonstrated, less ‘spring back’ happens and this results in a more stable compacted tablet.
The use of specialised elliptical head forms is currently the only way to achieve more dwell time without slowing down an existing press or upsizing punches – both of which will negatively impact tablet productivity.
Get it right early on
Producing quality tablets is both complex and challenging. To optimise tablet production and quickly produce mass robust tablets with tailor-made properties, every process must be considered, starting with the formulation. It is essential that manufacturers know what their formulations contain and their characteristics, as this will inform what tooling is specified and how it should be used. It is advisable to investigate these issues at the design stage so that they can be resolved before scale-up. This approach will help in ensuring proficient production of quality tablets.
About the author
Rob Blanchard works as a Research, Development & Quality Systems Manager at I Holland where he combines R&D with quality and coordinates I Holland’s close collaboration with various academic research bodies including Nottingham University. Rob has been instrumental in the development of various products designed to solve problems for tablet manufacturers such as wear resistance, corrosion resistance and anti-stick characteristics.
References
- [Internet]. Future Market Insights. 2019 [cited 30 August 2019]. Available from: https://www. futuremarketinsights. com/reports/oral-soliddosage- pharmaceuticalformulation- market
Issue
Related topics
Drug Manufacturing, Formulation, Impurities, Ingredients, Manufacturing