Paper reports on QbD in bilayer tablet development
Posted: 28 July 2023 | Catherine Eckford (European Pharmaceutical Review) | No comments yet
A paper has stated that applying the quality by design (QbD) principle during development of bilayer tablets will “help improve product design while also enhancing the quality, safety, and efficacy of drug products”.
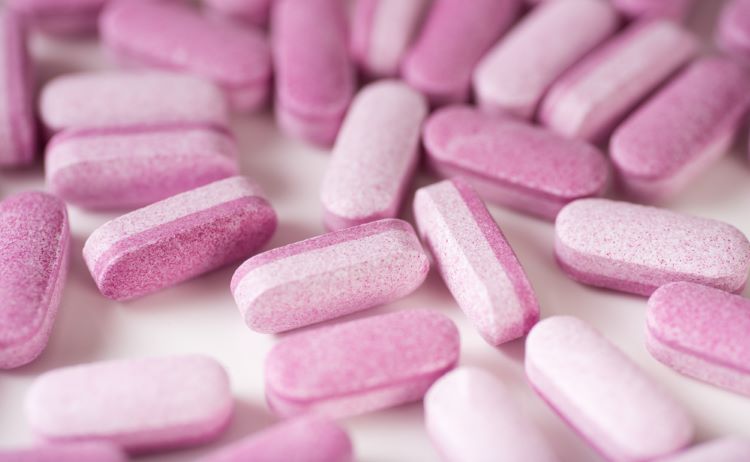
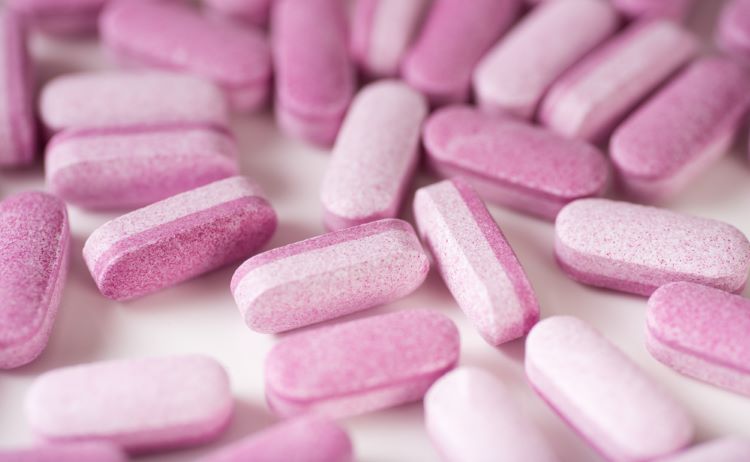
A research paper has reported a practical framework suitable for a systematic step-by-step quality by design (QbD) approach for the pharmaceutical development of bilayer tablets.
According to the authors, bilayer tablets have been considered one of the best options for the development of fixed-dose combination (FDC) formulations.
By delivering active substances, they can avoid incompatibilities in solubility, stability, and therapeutic efficacy in a single dosage form. They offer various drug release profiles for individual drugs incorporated in each layer of a bilayer tablet. This is rarely achievable by conventional tablets.
Successful manufacturing of these more complex dosage forms depends upon screening of material attributes of API and excipients. It also is dependable on the optimisation of processing parameters of individual unit operations of the manufacturing process. These processes must be strictly monitored and controlled to obtain an acceptable drug product quality and performance to achieve safety and efficacy per regulatory requirements.
However, while bilayer tablets are successful for the development of dual release tablets for the oral delivery of one or two drugs, formulations and manufacturing issues do exist.
Overcoming challenges during manufacture
Some of the main manufacturing challenges include segregation of the active ingredient from the blend, weight variation of layers, content variability of active ingredient(s) in different layers and delamination or separation of layers.
The paper noted that applying the QbD concept to optimise bilayer tablets might reduce the number of experiments required to produce a cost-effective drug product with extended-release properties.
Applying quality by design (QbD) to bilayer tablet development
QbD is a concept that is being increasingly adopted in pharma. The approach provides regulatory relief and flexibility, manages post-approval changes, and allows real-time quality control with a subsequent real-time release, the authors wrote.
An incomplete mechanistic understanding of the more complex manufacturing processes of bilayer tablet compression has encouraged researchers to implement the systematic QbD concept for bilayer tableting process development.
As such, the paper highlighted that the QbD-based concept has led to “remarkable progress” in developing bilayer tablets containing different drugs at different doses and release rates.
Approaches such as risk identification, analysis, and evaluation of critical material attributes (CMAs) and critical process parameters (CPPs) can help to overcome challenges in commercial manufacture of bilayer tablets, the paper reported. This is in respect to critical quality attributes (CQAs) through systematic risk assessment, along with the implementation of a control strategy for the implementation of QbD.
In addition, the authors stated that using near-infrared (NIR) and Raman spectroscopy as process analytical technologies (PATs), QbD/PAT has shown to be effective for the scale-up of bilayer tablets containing a low drug dose. Studying these approaches should be “priority in the pharmaceutical industry”.
Ultimately, Simão et al. reported that the design-based planning approach that QbD uses is a valuable strategy when working with bilayer tablet technology. “Employing this planned multivariate approach to bilayer tablet development will help improve product design while also enhancing the quality, safety, and efficacy of drug products.”
The research was published in European Journal of Pharmaceutical Sciences.