The importance of critical quality attributes in Quality by Design for rapid bioprocess development strategies
Posted: 15 December 2017 | Arathi Kizhedath, Jarka Glassey | No comments yet
QbD and PAT could revolutionise the way biopharma industries operate by cutting down their attrition rates, which could drastically change their business model. This article considers the issues involved.
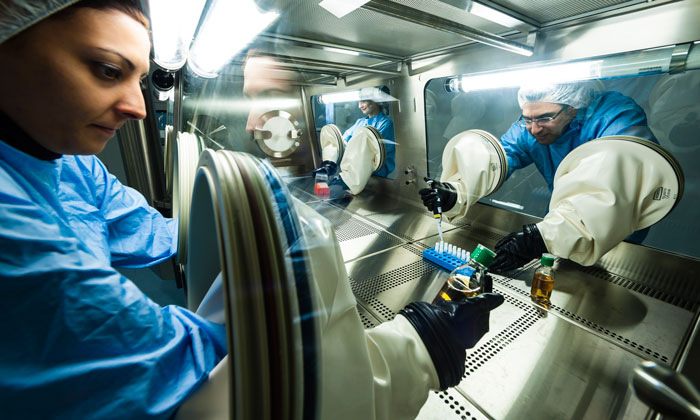
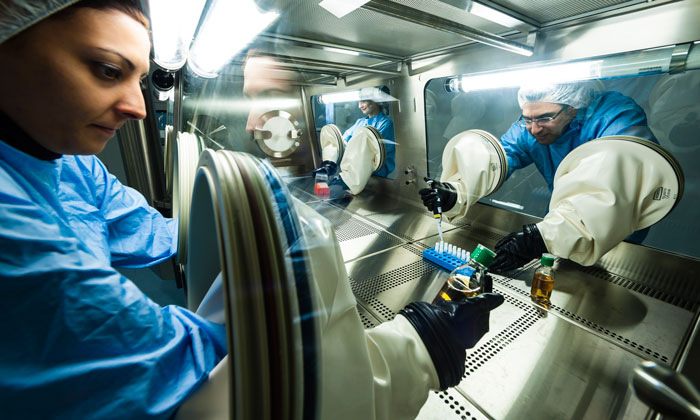
The pharmaceutical market is valued at $774bn and expected to reach $1.06tn by 2022.1 Biopharmaceuticals play an important role in this increase and their contribution is set to increase from 27% to 52% of world pharmaceutical sales, dominating the oncology and anti-rheumatics market until 2022, both in sales and R&D.1 Although the trends seem to be in favour of biopharmaceutical development, growth rates have not yet reached their full potential due to financial and technical complexities involved in the early stages of research and development, bioprocess development and preclinical testing.
Compared to the 21 biologics approved by the US Food and Drug Administration (FDA) in 2015, only 14 were approved in 2016, indicating a scarcity in innovation and lack of progress in bioprocess development strategies – mainly in early-stage screening and manufacturability. This, coupled with the looming second patent expiry cliff leading to the biosimilar boom, highlights a pressing need for rapid bioprocess development strategies and faster commercialisation. The aforementioned challenges are estimated to put around $200bn of sales at risk. Tackling these challenges will allow resources to be redirected into more innovation with a focus on drugs for rare and neglected diseases.
The need for Quality by Design (QbD) arose in early 2000, as the traditional approach to biopharmaceutical drug development was primarily empirical. This, combined with limited emphasis on process understanding, led to manufacturing failures and consequently increased product wastage. Furthermore, limited attention was given to the analysis of the root causes of these failures and to the prediction of scale-up effects on the final product quality and yield. Unlike conventional drugs, which mainly revolve around small-molecule chemistry, biological drugs are far more complex to produce and characterise as they are 200-1,000 times larger, structurally more complex and highly sensitive to their manufacturing conditions. The costs involved in development and production of biopharmaceutical entities are 1.5-2.5 times higher than that of small molecule drugs.2
The QbD paradigm
The concept of QbD was incorporated into the pharmaceutical manufacturing control review process in 2004, following the pharmaceutical cGMP for the 21st-century initiative (Figure 1). The main aim of the initiative was to harmonise and modernise the product, process and regulatory aspects of pharmaceutical manufacturing. The QbD paradigm urges industries to incorporate the following principles into their own process:
- Identify and have a better understanding of their product profile in terms of safety and efficacy
- Identify physical, chemical or microbiological properties that can affect safety and efficacy, and thus should be controlled within a predetermined range
- Design the process so as to deliver the required quality product consistently and control it by implementing a robust control strategy
- Validate, document and continuously monitor the process to make sure the system/bioprocess performs robustly over the product life cycle.3,4
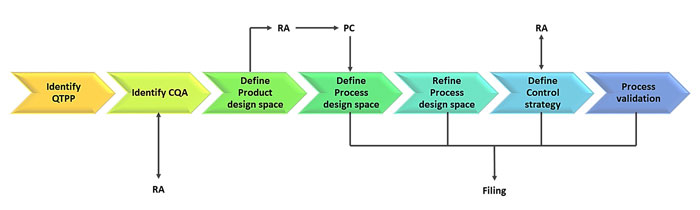
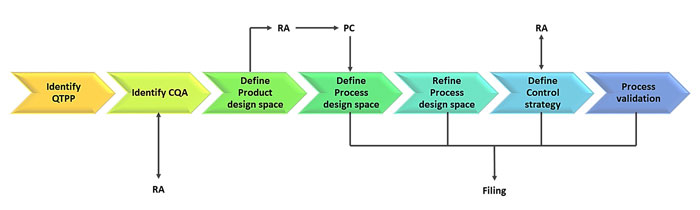
Figure 1: A schematic for Quality by Design in the biopharmaceutical industry.4 RA = risk assessment; PC = process characterisation
Recent studies reported that toxicity and lack of efficacy were the most important factors for high attrition rates in small molecule drug development.5 With nearly 80% of biological drugs failing in clinical development, mainly due to lack of efficacy and safety, smarter preclinical development using QbD-based approaches is urgently needed. This requires better product understanding, ie, examining characteristics that contribute to product quality, such as biological activity, affinity, pharmacology, toxicity, immunogenicity, etc, that can aid early prediction of success or failure. From a QbD point of view, this encompasses the principles of Quality Target Product Profile (QTPP) and Critical Quality Attributes (CQA). QTPP includes dosage form and strength, route of administration, intended use, release/delivery of therapeutic moiety, pharmacokinetics, and drug product criteria required for intended market (stability and purity). After the identification of QTPP, CQAs are then defined based on risk assessments. The rationale for identifying CQAs and relating them to product safety and efficacy arises from QTPP, prior product/process knowledge, literature, clinical data, non-clinical data including platform-based, in vivo as well as in vitro, assays, and relevant data from similar products. The main CQAs for biological drugs fall into the categories of size, charge, primary structure, post-translation modifications and higher order structure. For monoclonal antibodies, examples of product-related CQAs are fragmentation, aggregation, inadvertent glycosylation and conformation, whereas process-related CQAs are host cell proteins, formulation buffer components, and culture media residues, to name a few.6
QbD offers a plethora of advantages to the biopharmaceutical industry, as well as to regulatory agencies. It allows for easy implementation of innovative technologies, technical and scientific harmonisation of regulations, minimisation of manufacturing failures, reduction of attrition rates, as well as ensuring consistent production of high-quality products by continuously monitoring and updating bioprocesses. However, to exploit the full potential of QbD, many challenges must still be overcome, including filling terminology, training, fitting existing legacy products into the QbD frameworks, conflict of opinions among regulatory agencies across the world, and most importantly, a limited understanding of how CQAs impact the quality and efficacy of a product. A possible solution could be to increase the use of non-clinical studies as well as in silico tools to augment knowledge about the impact of CQAs on the clinical potency and safety of biological drugs.7 These rapid screening methods can be seamlessly integrated into a QbD approach when linked with the target product profile as well as critical quality attributes.
The BIORAPID approach
Expert panels consisting of members from industry and academia tried to address the above issues and underlined the crucial need to prepare academic education and training to expedite pharmaceutical process development as well as knowledge transfer pertaining to the latest advances in QbD and PAT. Although it resulted in highly successful training courses like M3C (measurement, modelling, monitoring and control), there still seemed to be a need for more in-depth training.8 Recognising the need to address the above challenges by implementing QbD and PAT as well as adequate training and knowledge transfer, BIORAPID – a European Union Horizon 2020 funded Marie Skłodowska-Curie Actions Innovative Training Network (MSCA ITN) – was formed to provide this training to early-stage researchers (ESRs). This enabled them to integrate directly into the European biopharmaceutical industry and implement state-of-the-art methods that uphold the QbD paradigm by providing a platform for rapid bioprocess development strategies for potential biopharmaceutical drug candidates (Figure 2). Though the framework was conceptualised with oncology-related proteins and recombinant proteins for diabetes treatment in mind, the resultant monitoring and modelling methods will be applicable to other biopharmaceutical process development. The four pillars of BIORAPID are rapid screening, modelling tools in bioprocess development, consistent development and scale-up, and real-time monitoring of bioprocesses. It also places specific emphasis on improving data quality, multivariate data analysis techniques, hybrid modelling, design of experiments, data augmentation, uncertainty and risk analysis, as well as workflow development, all of which are essential elements of the QbD toolbox.9 This is based on a strong academic and industrial foundation, with equal numbers of partners from industry and academia allowing for seamless knowledge transfer. What sets BIORAPID apart from other approaches is that it focuses on strategies that allow for rapid development of novel bioactive molecules from the very early stages of potency and efficacy testing to the biomanufacturing process characterisation and effective monitoring by hybrid modelling and multivariate approaches, which imparts a predictive nature to the platform.
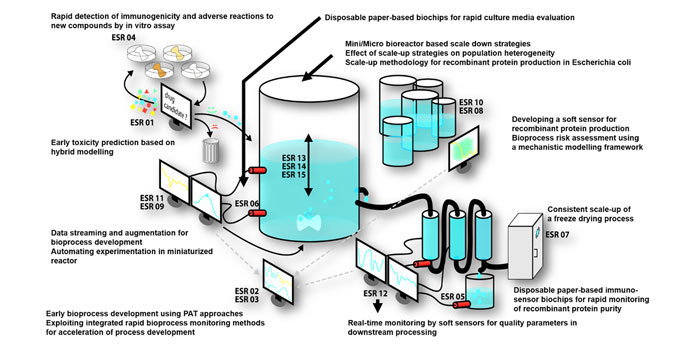
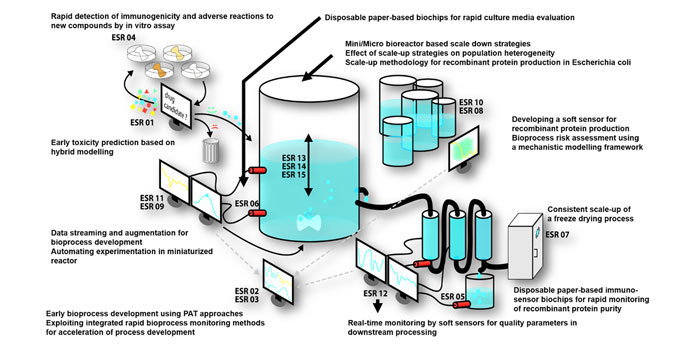
Figure 2: The BIORAPID framework, spanning the entire bioprocess development pipeline
Implementation of QbD and PAT could revolutionise the way biopharma industries operate by cutting down their attrition rates, which could drastically change their business model and enable them to save time, money and resources. This could lead to reduction of prices for biologic drugs as well as more focus on medicines for rare diseases, thus proving beneficial to society.
Acknowledgments
The authors gratefully acknowledge the financial support from the EU-Horizon 2020 Marie Skłodowska-Curie Actions Innovative Training Network (MSCA ITN) project BIORAPID (no. 643056). The authors acknowledge the support and guidance from all the Biorapid ESRs, scientists in charge and all the BIORAPID partners involved (Acreo Swedish ICTAB, Alcyomics, Chr. Hansen AS, Danmarks Tekniske Universitet, Fujifi lm Diosynth Biotechnologies, Linköping Universitet, Newcastle University, Sanofi Aventis Deutschland GmbH and Technische Universität Berlin).
References
- EvaluatePharma (2017) World Preview (2017) Outlook to 2022. 10th edition.
- Blackstone E, Fuhr J. Biopharmaceuticals: the economic equation. Biotechnol Healthc. 2007;4(6):41-45.
- Rathore AS. (2009) Roadmap for implementation of quality by design (QbD) for biotechnology products. Trends in biotechnology. 2009;27(9):546-553.
- Rathore AS, Winkle H. Quality by design for biopharmaceuticals. Nature biotechnology. 2009; 27(1):26.
- Waring MJ, et al. An analysis of the attrition of drug candidates from four major pharmaceutical companies. Nat Rev Drug Discov. 2015;14(7):475-486.
- Group CMCBW. A-Mab: a case study in bioprocess development. 2009. Emeryville, CA: CASSS.
- Kizhedath A, Wilkinson S, Glassey J. Applicability of predictive toxicology methods for monoclonal antibody therapeutics: status quo and scope. Archives of Toxicology. 2016:1-18.
- Bracewell D, et al. Report and recommendation of a workshop on education and training for measurement, monitoring, modelling and control (M3C) in biochemical engineering. Biotechnology journal. 2010;5(4):359-367.
- Herwig C, Glassey J, Kockmann N, Gernaey K, Barolo M. Better by Design. The Chemical Engineer. 2017;41-43.
Biography
Issue
Related topics
Biopharmaceuticals, Bioprocessing, Drug Development, Manufacturing, Process Analytical Technologies (PAT), Quality by Design (QbD)