Accelerating biomanufacturing with automated PAT systems
Posted: 2 August 2023 | Catherine Eckford (European Pharmaceutical Review) | No comments yet
Experts at Amgen have highlighted a micro sequential injection (µSI) process analyser and automatic assay preparation platform (A2P2) as an autonomous process analytical technology (PAT) platform to enable rapid testing and release of biopharmaceutical products.
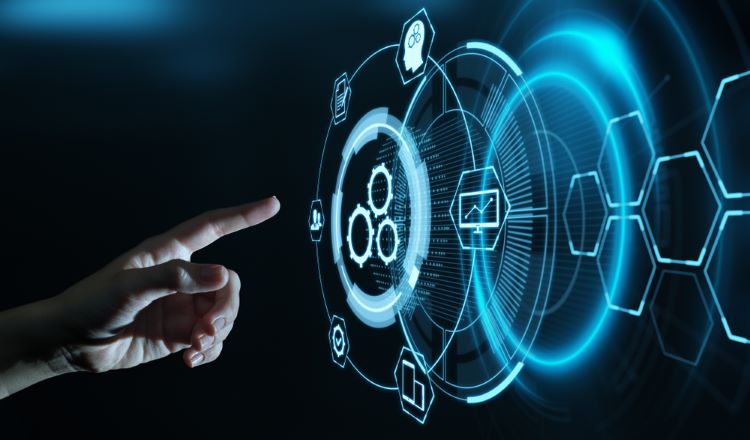
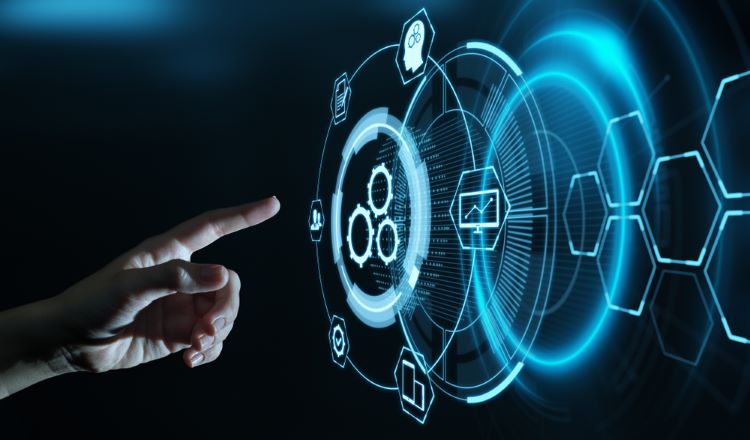
Research published in Biotechnology and Bioengineering has demonstrated two innovative, automatic, online, real-time sample acquisition and preparation systems for in-process monitoring, control, and release of biopharmaceuticals. The proposed autonomous process analytical technology (PAT) platform comprises of a micro sequential injection (µSI) process analyser and automatic assay preparation platform (A2P2) for use in the laboratory as an off-line analytical system and on the manufacturing floor. These can facilitate rapid testing and release of products manufactured in a good manufacturing practice (GMP) environment.
Real-time monitoring and control of the biomanufacturing processes through product quality insights continues to be a key area of focus in the biopharmaceutical industry, the paper reported.
Authored by experts at Amgen, the paper asserted that delays associated with off-line analytical testing can hinder the speed of process development. Therefore, analytical technologies are necessary to accelerate process development.
The authors explained that an innovative analytical strategy is essential for building resilience and managing risks in manufacturing quality as well as for gaining competitiveness in the industry.
In developing an analytical strategy, automated systems aim to enable routine and on-demand acquisition of key product quality and process performance attributes in laboratories and manufacturing facilities.
The autonomous PAT platforms proposed by the researchers offer 24/7 monitoring, reliable performance and resource agility. This is in contrast to traditional analytical approaches which involve sample acquisition and preparation workflows. These are typically liable to errors due to manual operations.
Micro sequential injection (µSI)
While chip-based fluidic miniaturisation has advantages including low material consumption and rapid analysis, minimising sample and reagent consumption to the nanolitre or lower range on a microfabricated scale can introduce errors, for instance, in sampling.
Therefore, designing an instrument that reduces sample and reagent consumption to a few microliters is more advantageous, Wu et al. wrote. These factors have led to a practical level of miniaturisation through the integrated µSI fluidic design.
According to the paper, this design maintains short fluidic conduit geometry instead of narrow ones, decreasing sample and reagent consumption without the inherent issues of microfabricated fluidic channels.
How was the autonomous PAT platform designed?
The team developed and deployed the LC-MS and LC integrated µSI process analyser systems for online multi-attribute method (MAM) assay and glycan measurements.
They also designed a turn-key A2P2 system to accelerate development of attribute-centric biotherapeutic manufacturing processes.
Fundamental design considerations for the systems included instrument footprint reduction, faster result turnaround, software-driven features, capability consolidation, plus a simplified operation capability.
The autonomous PAT platform includes fluidic conduits and strategically placed material handling mechanisms. These offer resource conservation, optimised assay efficiency, controlled conditions, reproducible results and long-term system robustness.
The system contains multiple functional unit operations. These work in unison through programmable algorithms to manage sample and reagent logistics, direct processes, and reactions. Overall, these enable self-directed assay protocol selection with rule-based parameter adjustment for optimal output.
They can inform process development through their ability to rapid execute complex assays, the paper stated.
The authors summarised that the systems can be readily integrated into a strategy, enabling real-time, attribute-focused process development, monitoring, and control in the biopharmaceutical industry.
“Efficiency gains through the integration of fluidic miniaturisation, autonomous diagnostics, and advanced analytics are substantial and lead to efficient development of processes that consistently manufacture high quality products,” Wu et al. concluded.
Related topics
Analytical techniques, Big Pharma, Biopharmaceuticals, Bioproduction, Drug Development, Drug Manufacturing, Manufacturing, Process Analytical Technologies (PAT), Proteins, QA/QC, Research & Development (R&D), Technology, Therapeutics