Is the pharmaceutical sector realising its potential for sustainable manufacturing?
Posted: 11 April 2024 | Eric Flynn (Siemens UK & Ireland) | No comments yet
Digitalisation could dramatically streamline the process of setting up and running pharmaceutical manufacturing processes, bringing sustainability and cost benefits, as Eric Flynn, Head of Pharmaceutical and Life Sciences at Siemens, explains.
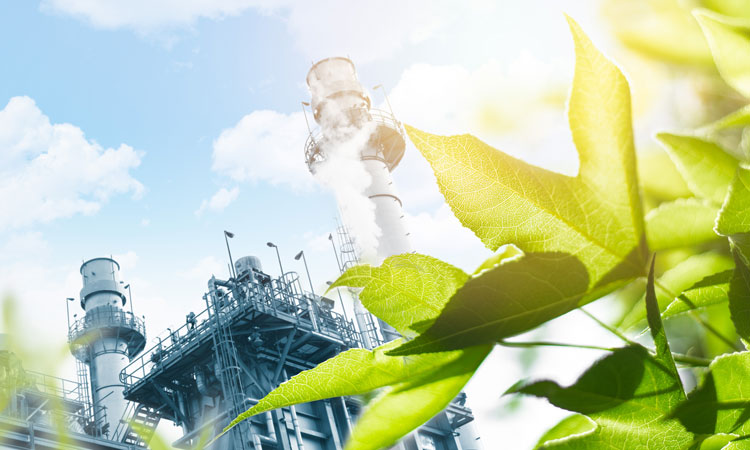
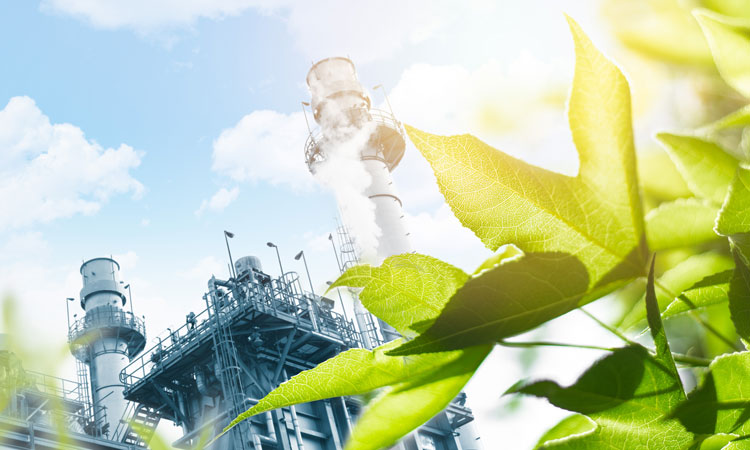
The pharmaceutical industry is becoming increasingly conscious of emissions and the importance of sustainable manufacturing.
Globally, the pharmaceutical sector emitted around 52 megatonnes of CO2 in 2015, the most recent period for which detailed numbers are available.1 That’s more than the automotive sector, which released 46.4 megatonnes in the same year, and the increased demand and complexity of medicines since then will only have swollen this figure.1
Every major pharmaceutical manufacturer in the UK and Ireland is investing in making their operations and supply chains more environmentally friendly. On-site renewable energy generation, waste reduction initiatives and tougher procurement protocols are becoming commonplace across the industry.
One area lacking major gains is in the process of design, engineering, commissioning and maintaining a manufacturing plant itself. Here, digitalisation promises to significantly reduce the environmental impact of these key stages of the process, while also unlocking greater process optimisation and sizeable financial savings.
However, changing long-standing and proven approaches to new product development across a whole sector is no small task. Much work remains to be done, and effective sharing of best practice across the industry and with academia will be crucial to success.
Collaborating for progress in sustainable manufacturing
This is a key aim of CPI’s Medicines Manufacturing Innovation Centre (MMIC), a Glasgow-based facility supported by collaborators including Siemens, GSK and AstraZeneca, among others. Creating more sustainable business processes is a pre-competitive activity; we all win when we make progress in sustainability and lose if we don’t.
The centre is helping to set out a vision for a more sustainable future for the sector, by working with businesses across the industry and giving them access to state-of-the-art facilities and academic knowledge. A large part of its mission is to help manufacturers across the industry work out how digitalisation could improve their performance – both environmentally and commercially.
Here are some of the key focuses that are making pharma manufacturing sustainable, greener, and leaner.
Doing more digitally
There is no getting around the fact that developing a manufacturing line that operates efficiently and delivers the highest quality product will always be an iterative process in which a series of prototypes are developed, tested and refined.
But as technology has advanced, we have arrived at a point where much of this work can be done virtually rather than with physical materials, saving time and material.
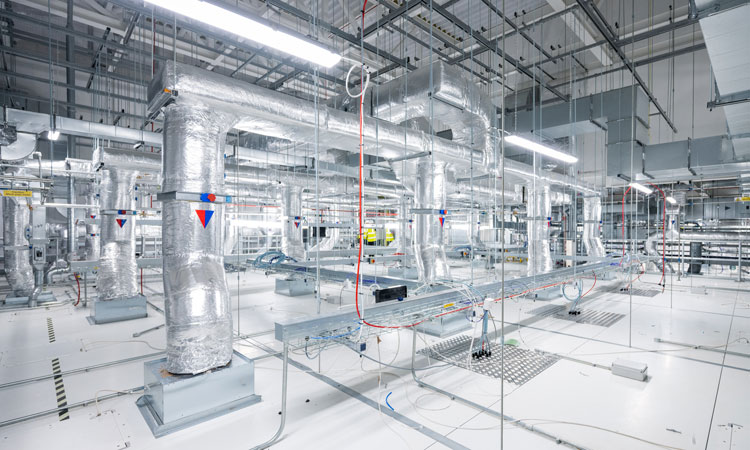
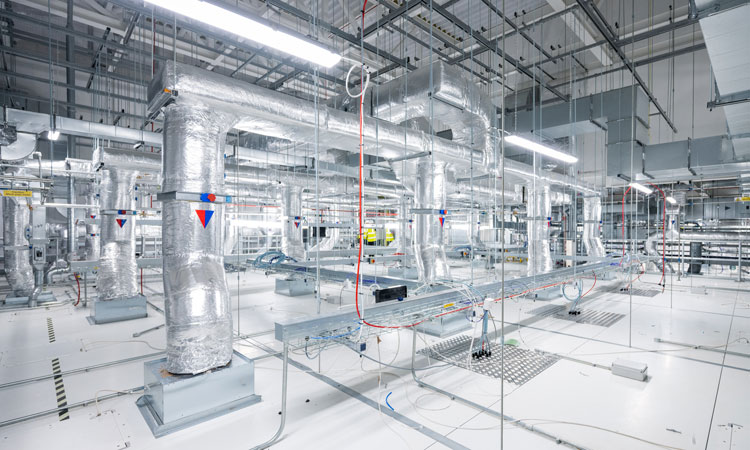
Credit: Siemens Plc
The industry can reorder the process towards design-test-make by moving from the current model towards an R&D approach based heavily on detailed virtual modelling. By doing the iterative design and engineering work in the virtual space, developers can implement a right-first-time philosophy and significantly reduce the number of physical prototypes that need to be built.
This translates into less consumption of physical materials, less energy used to manufacture physical prototypes, and less road distance for the logistics operation needed to ensure the right components are in the right place.
Further, the potential sustainability benefits of digital modelling continue far beyond the R&D phase by providing insight that can support a product across its entire manufacturing and supply chain.
Digital twinning for more sustainable production
With a digital twin, virtual modelling is combined with monitoring, analysis and simulation of a physical system, so the two are ‘twinned’.
By incorporating real-time data, the model better reflects the operation of every component of the process as it happens in reality. It can then predict precisely how manufacture will perform if any of the operating conditions are changed.
This is a game changer when it comes to optimising manufacturing operations. Instead of needing to experiment with physical tweaks and time-consuming, wasteful testing of the resulting products, again much of the trial and error can be conducted virtually, allowing engineers to arrive at an optimum process with much lower environmental and financial cost.
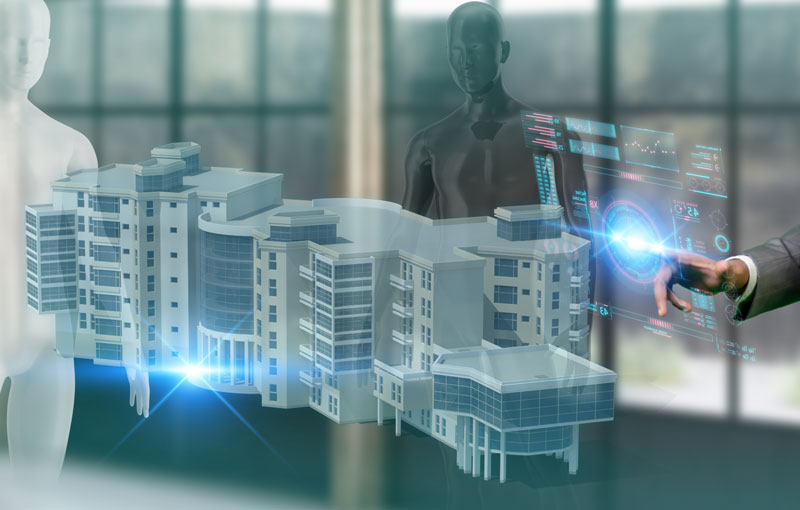
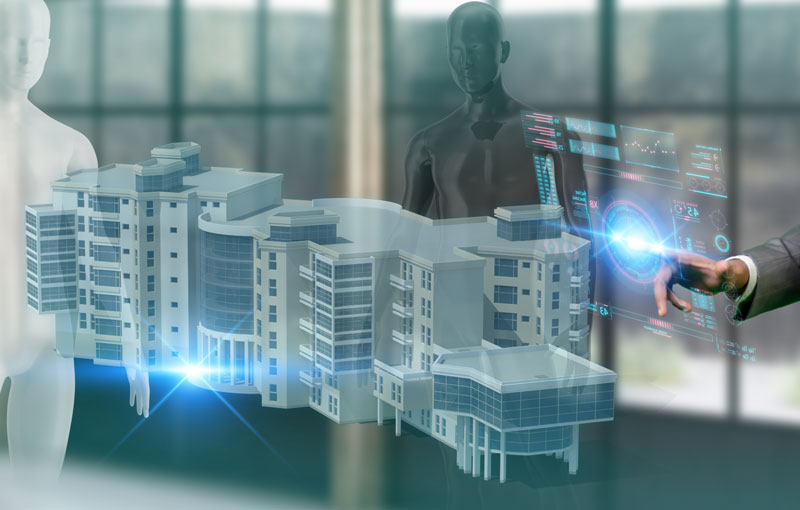
With a digital twin, virtual modelling is combined with monitoring, analysis and simulation of a physical system
Digital twinning can also potentially unlock a higher level of optimisation than was possible in the pre-digital era, both in terms of efficiency and process safety, because operators now have access to a far greater level of insight into the complex variables at play. This allows a more detailed understanding of exactly how different variables affect the outcomes. By integrating machine learning and other novel technologies, the staged implementation of digital twins also enables a robust pathway to the delivery of other future facing technologies and the sustainability benefits they’ll provide.
A further environmental benefit of digitalisation is the added flexibility it gives the workforce. Where once a site visit was the only way for somebody to interact with a process, whether as an engineer, inspector, trainee or in any other capacity, today digitalisation allows professionals to gain detailed insight remotely and together, via the data and visualisations available in the cloud.
This might mean a specialist based in another country or continent is able to provide useful guidance and explore system parameters without ever needing to take an international flight, both saving resources and reducing time to market.
Towards a greener future
With the pharmaceutical industry contributing such a significant amount to global emissions, there is a clear and urgent need for innovative thinking and major change to the way medicines are made. Digitalisation will play a fundamental role in making this possible, and industry-wide collaboration through initiatives such as those at CPI will be crucial.
The good news is that, in most cases, there is strong alignment between sustainability goals and the requirements of the Good Manufacturing Practice (GMP) regulations – and commercial imperatives around process optimisation and cost control. The stage is set for a green revolution in pharmaceutical manufacturing.
About the author
Eric Flynn is Head of Pharmaceutical and Life Sciences at Siemens UK & Ireland. He leads Siemens’ efforts to optimise and improve processes for clients within the pharmaceutical, biopharmaceutical and medical device sectors.
References
- Belkhir L, Elmeligi A. Carbon Footprint of the Global Pharmaceutical Industry and Relative Impact of Its Major Players. Journal of Cleaner Production [Internet]. 2019 Mar;214:185–94. Available from: https://www.sciencedirect.com/science/article/abs/pii/S0959652618336084
Related topics
Drug Manufacturing, Manufacturing, Research & Development (R&D), Sustainability, Technology
Related organisations
AstraZeneca, GSK, Medicines Manufacturing Innovation Centre (MMIC), Siemens